Home » Posts tagged 'phase 2'
Tag Archives: phase 2
EIDD-2173, ATI-2173, Fosclevudine alafenamide


EIDD-2173; also known as ATI-2173
Fosclevudine alafenamide
Phase 2
Molecular Weight | 529.45 |
---|---|
Formula | C22H29FN3O9P |
CAS No. | 1951476-79-1 |
Hepatitis B virus (HBV) is an infectious disease that targets the liver resulting in either an acute infection, with symptoms arising in 45 to 160 days, or a chronic infection, which 350 million people worldwide are affected by. Estimates indicate that 600,000 deaths occur each year as a result of consequences related to HBV infection. HBV possesses a 3.2- kb relaxed circular DNA (rcDNA) genome that is used to form covalently closed circular DNA (cccDNA) in a host cell. The cccDNA is then transcribed by RNA polymerase II, a host DNA-dependent RNA polymerase, to produce pregenomic RNA (pgRNA). The pgRNA is then used by the virally encoded reverse transcriptase to form rcDNA. The goals of current treatments for chronic HBV infections are to reduce HBV replication and reduce liver damage.
Current treatments for chronic HBV infections include pegylated alpha interferon and nucleoside/nucleotide reverse transcriptase inhibitors (NRTIs). NRTIs are converted to their corresponding 5 ‘-triphosphate, or diphosphate in the case of phosphonate containing NRTIs, and reduce viral replication by inhibiting the HBV encoded polymerase. Clevudine is an NRTI that is no longer being developed for the treatment of chronic HBV because of drug-related skeletal myopathy that was a result of mitochondrial dysfunction in patients.
Interestingly, clevudine triphosphate has been shown to be a competitive nonsubstrate inhibitor of the HBV encoded polymerase, and due to its long intracellular half-life, is able to suppress HBV replication for an extended period of time after drug withdrawal.
The discovery and synthesis of the (S,S) and (S,R) diastereomers of clevudine phosphoramidate has been previously reported. These studies were undertaken to address the myopathy concerns associated with clevudine. The phosphoramidate moiety was utilized to deliver clevudine, as its 5 ‘-monophosphate, to the liver reducing 1) systemic exposure to clevudine and 2) the possibility of skeletal myopathy. Both phosphoramidates showed anti-HBV activity similar to clevudine with the (S,S) diastereomer being slightly more potent.
SYN
See U.S. Patent No. 10,683,319.
PATENT
WO20 17223421
PATENT




EXAMPLE 11 :
[0374] Preparation of intermediate ATI-2173 from Compound-10.
[0375] Experimental Procedure
[0376] (H-l) Crude Compound-10 in THF (see Example 10) was divided into three aliquots and stirred with 2% HC1 aq. solution at pH 5-6, 4-5, and 3-4; for 16 h at 20-25 °C; the aliquots were combined and stirred at 15-20 °C for 72 h, with no degradation of ATI-2173 observed over the second time period;
[0377] (H-2) the pH of the mixture was adjusted to 7 with 7% NaHCCh;
[0378] (H-3) phase separation was carried out using 2-MeTHF, the organic phase was washed with NA2SO4 aqueous soltion, then concentrated to 1-3 V, and MTBE (5 V) was added; this operation was repeated twice;
[0379] (H-5) ATI-2173 was precipitated gradually upon addition of seed crystal and addition of n-heptane (5 V);
[0380] (H-6) the product was filtered; and
[0381] (H-7) the wetcake was dried, resulting in ATI-2173 in 99.73a% purity and
84.4% yield.
[0382] EXAMPLE 12:
[0383] Crystallization of ATI-2173
[0384] Initial studies examined the use of single or mixed solvent systems to crystalize the amorphous product, ATI-2173. Several solvent conditions were screened, including single solvent and mixed solvent systems, in order to determine the potential for obtaining a crystalline material from the amorphous material. None of the solvents tested worked and all conditions produced an oil product. The results are shown below in Tables 8 and 9.
[0385] Table 8: Single Solvent Systems


AS ON DEC2021 3,491,869 VIEWS ON BLOG WORLDREACH AVAILABLEFOR YOUR ADVERTISEMENT
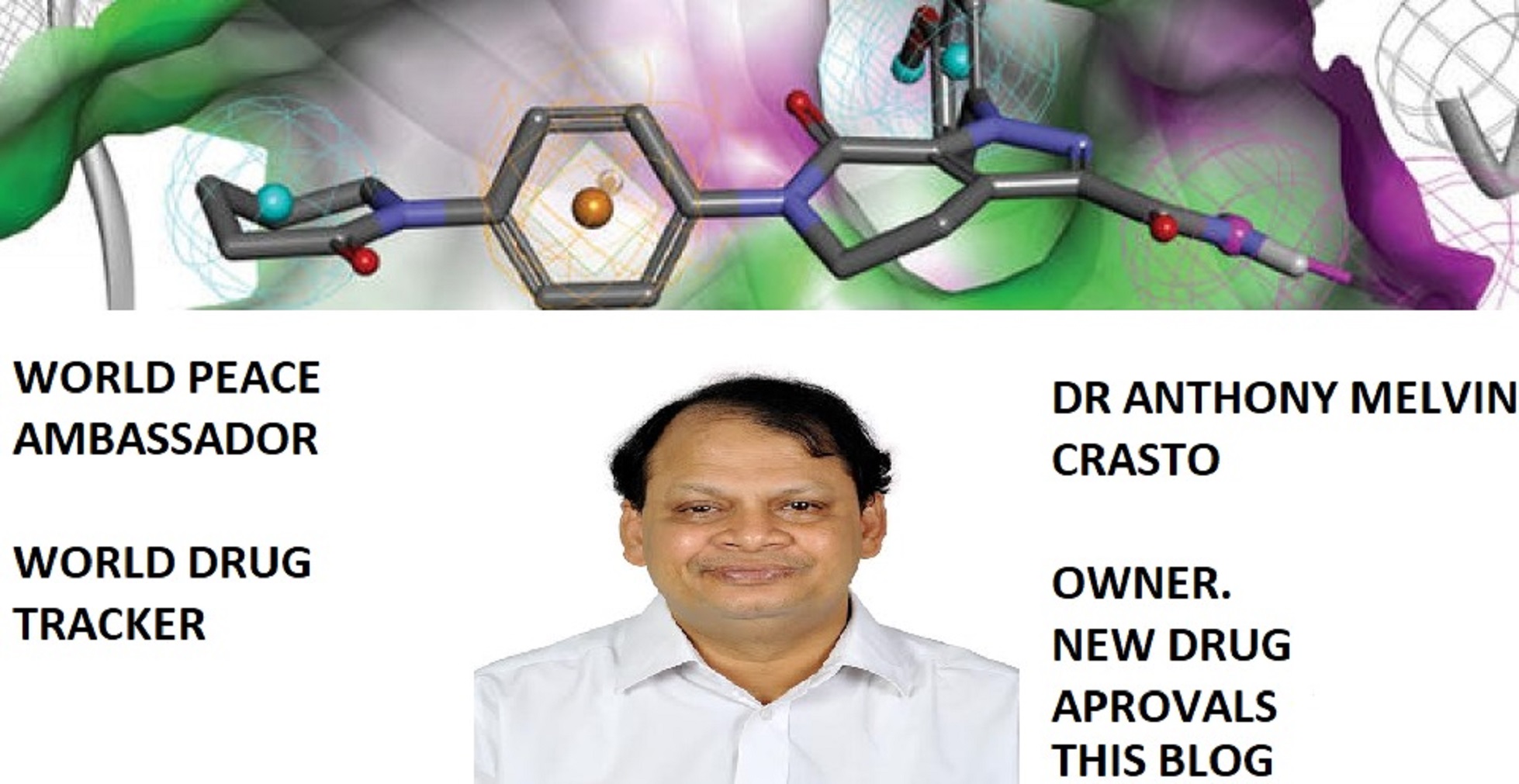
join me on Linkedin
Anthony Melvin Crasto Ph.D – India | LinkedIn
join me on Researchgate
RESEARCHGATE

join me on Facebook
Anthony Melvin Crasto Dr. | Facebook
join me on twitter
Anthony Melvin Crasto Dr. | twitter
+919321316780 call whatsaapp
EMAIL. amcrasto@amcrasto
///////////
////////// EIDD-2173, ATI-2173, EIDD 2173, ATI 2173, Hepatitis B virus, ANTI HBV, Fosclevudine alafenamide, PHASE 2

NEW DRUG APPROVALS
ONE TIME
$10.00
MAVORIXAFOR
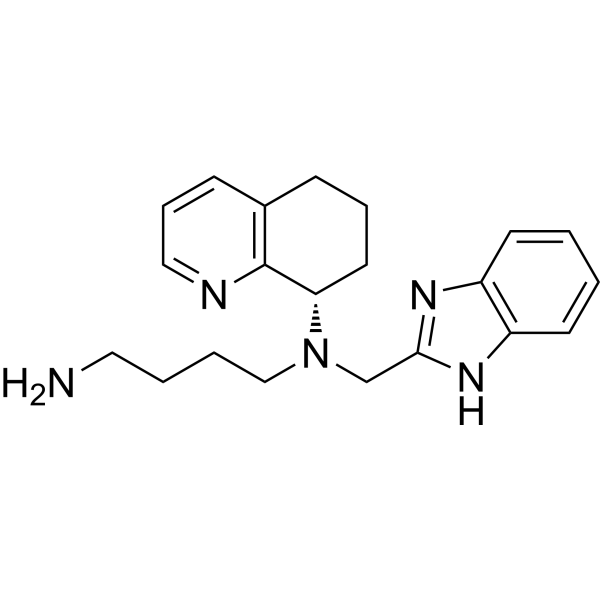
MAVORIXAFOR
AMD 070
N1-(1H-BENZIMIDAZOL-2-YLMETHYL)-N1-((S)-5,6,7,8-TETRAHYDROQUINOLIN-8-YL)-BUTANE-1,4-DIAMINE
fda approved 4/26/2024, To treat WHIM syndrome (warts, hypogammaglobulinemia, infections and myelokathexis), Xolremdi
Mavorixafor (AMD-070) is a potent, selective and orally available CXCR4 antagonist, with an IC50 value of 13 nM against CXCR4 125I-SDF binding, and also inhibits the replication of T-tropic HIV-1 (NL4.3 strain) in MT-4 cells and PBMCs with an IC50 of 1 and 9 nM, respectively.
Molecular Weight | 349.47 |
---|---|
Appearance | Solid |
Formula | C21H27N5 |
CAS No. | 558447-26-0 |
SMILES | NCCCCN(CC1=NC2=C(N1)C=CC=C2)[C@@H]3C4=C(CCC3)C=CC=N4 |
PHASE 2
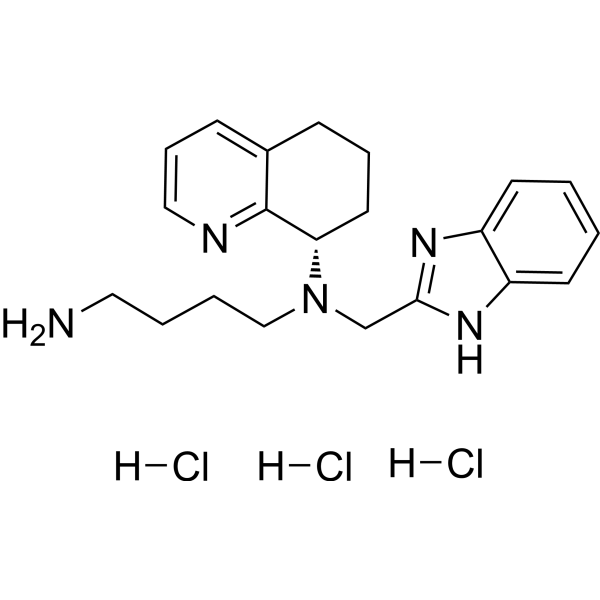
Mavorixafor trihydrochloride
Molecular Weight | 458.86 |
---|---|
Appearance | Solid |
Formula | C21H30Cl3N5 |
CAS No. | 2309699-17-8 |
SMILES | [H]Cl.[H]Cl.[H]Cl.NCCCCN(CC1=NC2=CC=CC=C2N1)[C@@H]3C4=NC=CC=C4CCC3 |
AMD-070 is a small molecule drug candidate that belongs to a new investigational class of anti-HIV drugs known as entry (fusion) inhibitors. Approximately 76% of HIV-patients with measurable viral load are infected with a strain of virus that is resistant to one or more classes of antiretroviral agents, thus reducing treatment options. Unlike many existing HIV drugs that target the virus after it has infected a healthy cell, AMD-070 blocks the virus from entering a healthy cell, thus preventing the replication process. AMD-070 targets the CXCR4 receptor on HIV and prevents the virus from entering and infecting healthy cells. AMD-070 is specific for the CXCR4 receptor and does not interact with any other chemokine receptors in vitro. AMD-070 strongly inhibits viral infection by all CXCR4 using virus (including virus using CXCR4 alone and/or virus using CXCR4 and CCR5) in vitro. AMD-070 is orally bioavailable in animals, it has suitable PK and toxicity profile for oral dosing. AMD-070 shows additive or synergistic effects in vitro in combination with other known anti-HIV agents. AMD-070 is active against CXCR4 using HIV strains that are resistant to existing antiretroviral therapies in vitro, reveals potent anti-HIV activity against CXCR4-using laboratory strains and clinical isolates. MD-070 had been in phase II clinical trials by Genzyme for the treatment of HIV infection. However, this research has been discontinued. AMD-070 has been studied in Phase I/II clinical trials for the treatment of Renal cell carcinoma and Phase I clinical trials for the treatment of malignant melanoma and solid tumours.
PAPER
https://pubs.acs.org/doi/10.1021/acs.oprd.2c00076
Org. Process Res. Dev. 2022, 26, 6, 1831–1836
A novel and practical synthesis of mavorixafor (1) is reported. The novelty of this synthetic route is the use of 8-chloro-5,6,7,8-tetrahydroquinoline (9) and 1,4-diaminobutane as the materials, instead of 8-amino-5,6,7,8-tetrahydroquinoline (4) and N,N-diprotected aminobutyraldehyde (6a or 6b). The preparation of (S)-8-(4-aminobutylamino)-5,6,7,8-tetrahydroquinoline (13) by resolution with N-acetyl-l-leucine was first achieved. Then the one-pot synthesis of 1 from 13 involving protection, condensation, and subsequent hydrolysis was successfully developed. In addition, the final product with a satisfactory purity (>99.5%, detected by both achiral and chiral HPLC) was obtained by a simple operation (salification) without column chromatographic purification.





NEW PAT
Scheme I


Mavorixafor


EXEMPLIFICATION
Example 1: Synthesis of Sulfonate adduct F-2d:
Scheme V:
1) AcOH, NaCI, water 1) Na 2 S 2 O 5 , THF, water
2) n-Heptane, THF 2) THF/n-heptane, acetonitrile
Step 1C Step 1 D


Step 1A: Preparation of Dl
Charge diethyl-4-aminobutyl acetal (E) (1.00 wt, 1.00 eq) to vessel A. Charge acetonitrile (10.0 vol, 7.8 wt) and adjust temperature to 20°C. Heat the mixture to 40°C. Concentrate the reaction mixture to 6.0 vol under reduced pressure at 35 to 45°C.
[0098] Acetonitrile filler (5.0 vol, 3.9wt) at 35 to 45°C. Concentrate the reaction mixture to 6.0 vol under reduced pressure 35 to 45°C. This step is repeated once as described below.
[0099] Acetonitrile filler (5.0 vol, 3.9wt) at 35 to 45°C. Concentrate the reaction mixture to 6.0 vol under reduced pressure at 35 to 45°C. Cool to 20°C.
[00100] Charge di-tert-butyl dicarbonate (1.1 eq, 1.5 wt) to a drum, followed by acetonitrile (0.4 vol, 0.3 wt) and agitate until fully dissolved. Concentrate the reaction mixture to 6.0 vol under reduced pressure at 35 to 45°C.
[00101] Charge this di-tert-butyl dicarbonate solution in acetonitrile to vessel A maintaining 20°C. Charge acetonitrile (1.5 vol, 1.1 wt) to the solution as a line rinse and stir at 20°C for 30 to 60 min..
[00102] Charge 4-dimethylaminopyridine (0.076 wt, 0.10 eq) to the vessel A at 20°C. Heat the solution to 40°C. Concentrate the reaction mixture to 5.0 vol under reduced pressure. Charge acetonitrile (5.0 vol, 3.9 wt) to the solution. Concentrate the reaction mixture to 5.0 vol under reduced pressure.
[00103] Take the resulting solution of Dl into next reaction without isolation.
Step IB: Preparation of Cl
[00104] Charge acetonitrile (2.0 vol, 1.6 wt) at 35 to 45°C to vessel A containing solution of D-1 from Step 1A.
[00105] Charge di-tert-butyl dicarbonate (1.4 eq, 1.9 wt) to a drum, followed by acetonitrile (10.0 vol, 7.8 wt) and agitate until fully dissolved. Charge this di-tert-butyl dicarbonate solution to vessel A, 2 to 6 h while distilling under vacuum at 35 to 45°C maintaining the volume of the reaction at 7.0 vol. Load acetonitrile (3.0 vol, 2.4 wt) over 20 to 40 min. as a line rinse while distilling under vacuum at 35 to 45°C, maintaining the volume of the reaction at 7.0 vol.
[00106] Charge di-tert-butyl dicarbonate, (0.14 eq, 0.19 wt) to a drum, followed by acetonitrile (1.0 vol, 0.74 wt) and agitate until fully dissolved. Charge this di-tert-butyl dicarbonate solution to vessel A over 20 to 40 min.. Charge acetonitrile (0.3 vol, 0.24 wt) over 10 to 20 min as a line rinse while distilling under vacuum at 35 to 45°C, maintaining the volume of the reaction at 7.0 vol.
[00107] Concentrate the reaction mixture to 5.0 vol distilling under vacuum at 35 to 45°C.
[00108] Charge n-heptane, (7.5 vol, 5.1 wt) to the reaction mixture, and concentrate the reaction mixture to 5.0 vol under reduced pressure at 40°C. This step is repeated once as described below.
[00109] Charge n-heptane, (7.5 vol, 5.1 wt) to the reaction mixture, and concentrate the reaction mixture to 5.0 vol under reduced pressure at 40°C.
[00110] Charge decolorizing, activated charcoal (0.2 wt) to the solution and stir for 1 to 2 h at 40°C. Filter the reaction mixture at 40°C. Charge n-heptane, (2.0 vol, 1.4 wt) to the reactor vessel and stir for 5 to 15 min. at 20°C before charging to the filter as a line rinse. Combine the filtrate and wash, and as required adjust to 20°C.
[00111] Take the resulting solution of Cl into next reaction without isolation.
Step 1C: Preparation of Bl
[00112] Charge 15% v/v acetic acid (2.0 vol) caution gas evolution, to vessel A containing solution of Cl from Step IB, maintaining the temperature at 20°C and stir for 10 min. at 20°C. Allow the phases to separate for 15 min. at 20°C. Discharge the aqueous phase to waste, retaining the organic phase in vessel A. This step is repeated once as described below.
[00113] Charge 15% v/v acetic acid (2.0 vol) maintaining 20°C and stir for 10 min. at 20°C. Allow the phases to separate for 15 min. at 20°C. Discharge the aqueous phase to waste, retaining the organic phase in vessel A.
[00114] Adjust the reaction to 30°C. Charge 4% w/w sodium chloride solution (2.1 vol) to the vessel maintaining the temperature at 30°C. Charge glacial acetic acid (4.1 vol, 4.3 wt) to the vessel maintaining 30°C. Stir the reaction mixture for 2 h maintaining the temperature at 30°C.
[00115] Charge purified water, (6.0 vol) at 30°C. Stir the contents for 5 to 10 min. at 30°C, and separate the phases, retaining the upper organic phase in vessel A. Charge the lower aqueous phase to vessel B.
[00116] Charge purified water (4.0 vol) at 30°C and stir for 5 to 10 min. maintaining the temperature at 30°C. Separate the phases at 30°C, retaining the upper organic phase in vessel A. Charge the lower aqueous phase to vessel B.
[00117] Adjust the temperature to 30°C of vessel B containing combined aqueous phases. Charge n-heptane, (2.0 vol, 1.4 wt) to vessel B and stir for 5 to 10 min. maintaining the temperature at 30°C. Separate the phases at 30°C, over 15 min.. Charge the upper organic phase to vessel A and recharge the lower aqueous phase to vessel B. This step is repeated two additional times as described below.
[00118] Charge n-heptane, (2.0 vol, 1.4 wt) to vessel B and stir for 5 to 10 min. maintaining the temperature at 30°C. Separate the phases at 30°C, over 15 min.. Charge the upper organic phase to vessel A and recharge the lower aqueous phase to vessel B.
[00119] Charge n-heptane, (2.0 vol, 1.4 wt) to vessel B and stir for 5 to 10 min. maintaining the temperature at 30°C. Separate the phases at 30°C, over 15 min., discharge the lower aqueous phase to waste and charge the upper organic layer to vessel A.
[00120] Concentrate the combined organic phases in vessel A to 3.0 vol at 10 to 20°C under reduced pressure. Offload the solution to new HDPE drum(s) and line rinse with n-heptane (0.5
vol, 0.4 wt) at 20°C. Homogenize the drum and store as “Bl solution in n-heptane,” and take into next reaction without isolation.
Step ID: Preparation of F-2d
[00121] Calculate a new 1.00 wt based on the above assay.
[00122] Charge “Bl solution in n-heptane” from Step 1C (1.00 wt, 1.00 eq, corrected for w/w assay, ca. 3.0 vol), into an appropriate vessel. THF load (3.0 vol, 2.7 wt). Heat the reaction mixture to 40°C.
[00123] Charge purified water, (0.02 vol, 0.02 wt) followed by sodium metabisulphite, (0.125 eq, 0.08 wt) as a solid via the charge hole at 40°C. Stir the resulting mixture for 30 to 35 min. at 40°C. This step was repeated four additional times to add the reagent in five portions total, as detailed below.
[00124] Charge purified water, (0.02 vol, 0.02 wt) followed by sodium metabisulphite, (0.125 eq, 0.08 wt) as a solid via the charge hole at 40°C. Stir the resulting mixture for 30 to 35 min. at 40°C.
[00125] Charge purified water, (0.02 vol, 0.02 wt) followed by sodium metabisulphite, (0.125 eq, 0.08 wt) as a solid via the charge hole at 40°C. Stir the resulting mixture for 30 to 35 min. at 40°C.
[00126] Charge purified water, (0.02 vol, 0.02 wt) followed by sodium metabisulphite, (0.125 eq, 0.08 wt) as a solid via the charge hole at 40°C. Stir the resulting mixture for 30 to 35 min. at 40°C.
[00127] Charge purified water, (0.02 vol, 0.02 wt) followed by sodium metabisulphite, (0.125 eq, 0.08 wt) as a solid via the charge hole at 40°C. Stir the resulting mixture for 36 hours at 40°C.
[00128] Cool the reaction mixture to 20°C over 3 to 4 h at a target constant rate. Filter the reaction mixture at 20°C on a 1-2 pm cloth.
[00129] Wash the solid with a pre-mixed mixture of THF (0.5 vol, 0.5 wt) and n-heptane (0.5 vol, 0.3 wt) maintaining the temperature at 20°C. This step was repeated an additional three times, as detailed below.
[00130] Wash the solid with n-heptane, (2.0 vol, 1.4 wt) as a line rinse and apply to the filtercake at 20°C.
[00131] Wash the solid with n-heptane, (2.0 vol, 1.4 wt) as a line rinse and apply to the filtercake at 20°C.
[00132] Wash the solid with acetonitrile, (2.0 vol, 1.6 wt) as a line rinse and apply to the filtercake at 20°C.
[00133] Dry the solid at 38°C under a flow of nitrogen for 12 h.
[00134] Determine residual solvent content. Pass criteria acetonitrile <2.0% w/w, n-heptane <2.0% w/w and tetrahydrofuran <2.0% w/w.
[00135] Yield of compound F-2d: 52-69%.
[00136] ‘H NMR (400 MHz, d 6 -DMSO): 8 5.22 (s, 1H), 3.77 (s, 1H), 3.45 (t, 2H), 1.70 (m, 2H), 1.44 (m, 20H) ). 13 C NMR (400 MHz, d 6 -DMSO): 8 152.6, 83.2, 82.0, 46.5, 29.6, 28.1, 26.0. FTIR (wavenumber, cm’ 1 ) 3294, 1721, 1738, 1367, 1233, 1180, 1135, 1109, 1045.
Example 2: Synthesis of F-3a:
Scheme VI:


Step 2A: Preparation of Gl
[00137] Charge J, (1.00 wt, 1.00 eq) to vessel A. Charge purified water, (1.0 vol, 1.0 wt) to vessel A and as necessary adjust the temperature to 20°C. Charge concentrated hydrochloric acid, (4.0 eq, 3.0 vol, 3.6 wt) to vessel A maintaining the temperature at 20°C. Line rinse with purified water, (0.5 vol, 0.5 wt) maintaining the contents of vessel A at 15 to 25°C.
[00138] Charge chloroacetic acid, (1.3 wt, 1.5 eq) and purified water, (1.0 vol, 1.0 wt) to vessel B and as necessary, adjust the temperature to 20°C. Stir until fully dissolved, expected 10 to 20 min.
[00139] Charge the chloroacetic acid solution to vessel A maintaining the temperature of vessel A at 20°C. Line rinse vessel A with purified water, (0.5 vol, 0.5 wt) at 15 to 25°C and charge to vessel B at 20°C. Heat the reaction mixture to 80°C. Stir the reaction mixture at 80°C for 20 h.
[00140] Cool the reaction mixture to 10°C over 1.5 h. Load 47% w/w potassium phosphate solution (6.0 vol) over 60 min. targeting a constant rate maintaining 10°C. Adjust the pH of the reaction mixture by charging 47% w/w potassium phosphate solution to pH 7.0 maintaining the reaction temperature at 10°C. Expected charge is 2.0 to 3.5 vol 47% w/w potassium phosphate solution.
[00141] Stir the slurry for >30 min. maintaining 10°C and rechecking the pH, pass criterion pH 7.0. Filter the reaction mixture through 20 pm cloth at 10°C. Wash the filter-cake with purified water, (1.0 vol, 1.0 wt) at 10°C. This step is repeated additional three times as described below.
[00142] Slurry wash the filter-cake in the reactor vessel with purified water, (10.0 vol, 10.0 wt) for 45 min. to 90 min. at 10°C. Filter the mixture through 20 pm cloth at 10°C.
[00143] Slurry wash the filter-cake in the reactor vessel with purified water, (10.0 vol, 10.0 wt) for 45 min. to 90 min. at 10°C. Filter the mixture through 20 pm cloth at 10°C.
[00144] Slurry wash the filter-cake in the reactor vessel with purified water, (10.0 vol, 10.0 wt) for 45 min. to 90 min. at 10°C. Filter the mixture through 20 pm cloth at 10°C.
[00145] Wash the filter-cake with purified water, (1.0 vol, 1.0 wt) at 10°C. The filter-cake was washed with purified water additional five times as described below.
[00146] Wash the filter-cake with purified water, (1.0 vol, 1.0 wt) at 10°C.
[00147] Wash the filter-cake with acetonitrile, (2×1.3 vol, 2×1.0 wt) at 10°C.
[00148] Dry the filter-cake on the filter under vacuum and strong nitrogen flow through the filter cake at 20°C until the water content is <15.0% w/w by Karl-Fisher analysis.
[00149] Dry the filter-cake on the filter under vacuum and strong nitrogen flow through the filter cake at 30°C until the water content is <5.0% w/w by Karl-Fisher analysis.
[00150] Dry the filter-cake on the filter under vacuum and strong nitrogen flow through the filter cake at 50°C until the water content is <1.0% w/w by Karl-Fisher analysis.
[00151] Yield of compound Gl: about 75%.
Step 2B: Preparation of F-3a
Charge di-/c/7-butyl dicarbonate, (1.85 wt, 1.4 eq) to vessel A followed by N,N-dimethylformamide, (2.6 wt, 2.7 vol) and stir at 20°C for 20 min. until dissolution achieved. Add A,A-diisopropylethylamine, (0.08 wt, 0.11 vol, 0.1 eq) to contents of vessel A at 20°C. Heat the contents of vessel A to 40°C.
[00153] Charge Gl, (1.00 wt) to vessel B followed by YW-di methyl form am ide, (5.2 wt, 5.5 vol) and adjust to 14°C.
[00154] Charge the Gl/DMF solution from vessel B to vessel A over 5 h at 40°C, at an approximately constant rate. Line rinse with Y,Y-di methyl form am ide, (0.4 wt, 0.4 vol), maintaining vessel A at 40°C. Stir the resulting reaction mixture at 40°C for 16 h.
[00155] Charge decolorizing charcoal activated, (0.20 wt). Adjust the mixture to 40°C and stir at 40°C for 60 to 90 min..
[00156] Clarify (filter) the reaction mixture into vessel B at 40°C. Charge N,N-dimethylformamide, (0.9 wt, 1.0 vol) via vessel A and filter at 40°C. Charge purified water, (3.5 vol) to the combined filtrates, over 60 min., maintaining the temperature at 40°C. As required, cool the mixture to 35°C over 30 to 60 min..
[00157] Filler F-3a, (0.02 wt) as seed material at 35°C. Stir at 34°C for 1.5 h then check for crystallization. Cool slurry to 30°C over 40 min.
[00158] Filler F-3a, (0.02 wt) as seed material at 30°C. Stir at 30°C for 1.5 h then check for crystallization.
[00159] Cool slurry at 20°C over 3.5 h at a targeted constant rate. Stir at 20°C for 3 hours. Charge purified water, (1.0 vol), maintaining the temperature at 20°C over 60 min..
Stir at 20°C for 3 hours.
[00160] Cool slurry to 2°C over 2.5 h. Stir at 2°C for 2.5 hours. Filter through 20 pm cloth and pull dry until no further filtrate passes. Wash the solid with pre-mixed Y,Y-di methyl form am ide / purified water, (2.0 vol, 1:2 v:v) at 2°C. Wash the solid with purified water, (2 x 3.0 vol) at 2°C. Dry under vacuum at 28°C until KF <0.2% w/w, and Y,Y-di methyl form am ide <0.4% w/w.
[00161] Yield of compound F-3a: 62-70%.
Example 3: Synthesis of Mavorixafor:
Scheme VI:

nce
Step 3A: Preparation of imine Q-1
[00162] To vessel A charge purified water, (8.7 vol, 8.7 wt) followed by potassium phosphate, (5.52 eq, 5.3 wt) portion-wise and cool to 15°C. Charge tetrahydrofuran, (4.3 vol, 3.8 wt) and n-heptane, (2.2 vol, 1.5 wt) to vessel A and cool the biphasic mixture to 0°C. Charge Fl, (1.00 eq, 1.00 wt) to the vessel in 2 portions maintaining 0°C.
[00163] Charge F-2d, (1.10 eq, 1.95 wt) to the vessel in 4 portions maintaining 0°C, ensuring portions are spaced by 10 min.. Stir the resulting biphasic mixture for 1.5 h at 0°C. Allow the layers to separate for 45 min. at 0°C before separating the layers. Retain the upper organic phase within vessel A.
[00164] Take the resulting solution of Ql into next reaction without isolation.
Step 3B: Preparation of amine P-1
[00165] To vessel B, charge tetrahydrofuran, (6.0 vol, 5.3 wt) and adjust to 15°C. Charge zinc chloride, (1.5 eq, 0.92 wt) to vessel B in 4 portions, maintaining 10 to 30°C. Adjust the reaction mixture in vessel B to 15°C. Stir the mixture at 15°C for 1 hour. Charge sodium borohydride,(1.0 eq, 0.17 wt) to vessel B in 2 portions maintaining 15°C. Cool the reaction mixture in vessel B to 15°C. Stir the mixture for 1 hour maintaining 15°C. Cool the reaction mixture in vessel B to -5°C.
[00166] Cool the retained organic solution of Ql in vessel A, from Step 3A, to -5°C.
[00167] Charge the organic solution in vessel A into vessel B over 1 to 2 h maintaining -5°C. Charge tetrahydrofuran, (1.0 vol, 0.9 wt) to vessel A as a line rinse and adjust to -5°C. Transfer the contents of vessel A to vessel B maintaining -5°C.
[00168] Stir the resulting reaction mixture in vessel B for 1.5 h maintaining -5°C.
[00169] Charge purified water, (4.5 vol, 4.5 wt) and glacial acetic acid, (1.0 eq, 0.27 wt, 0.26 vol) to the cleaned vessel A and cool to 0°C. Charge the contents of vessel B to vessel A over 1 to 2 h maintaining 0°C. Charge tetrahydrofuran, (1.0 vol, 0.9 wt) to vessel B as a vessel rinse, cool to 0°C and transfer to vessel A maintaining 0°C.
[00170] Warm the resulting mixture in vessel A to 30°C. Stir the resulting mixture in vessel A at 30°C for 1 h. Allow the layers to settle for 15 min. at 30°C before separating the layers. Retain the upper organic phase.
[00171] Cool the retained organic phase to 15°C. Charge to the vessel 25% w/w ammonia solution (3.0 vol) at 10 to 30°C. Cool the reaction mixture to 20°C. Charge to the vessel 25% w/w ammonium chloride solution (3.0 vol) at 20°C and stir for 1 h. Separate the layers for 15 min. at 20°C, retain the upper organic phase. Wash the retained organic phase with 10% w/w sodium chloride solution (3.0 vol) at 20°C for 10 min.. Allow the layers to settle for 10 min. at 20°C before separating and retaining the upper organic phase within the vessel.
[00172] Charge tert-butyl methyl ether, (0.5 vol, 0.4 wt) to the organic phase. Cool the mixture to 5°C. Adjust the pH of the reaction mixture to pH 5 with hydrochloric acid aqueous solution (expected ca. 9.0 vol) over 1 h at a targeted constant rate at 5°C. Stir the mixture at 5°C for 45 min.. Measure the pH of the aqueous phase to confirm the value is pH 5.
[00173] Charge sodium chloride, (2.1 wt) to the reaction mixture at 5°C and stir the mixture until everything is dissolved. Adjust the temperature of the reaction mixture to 20°C. Separate the layers at 20°C and retain the organic phase within the vessel. Tetrahydrofuran charge, (1.5 vol, 1.3 wt) maintaining 20°C.
[00174] Charge to the vessel 24% w/w sodium chloride solution (7.5 vol) at 20°C and stir for 10 min.. Separate the layers at 20°C and retain the organic phase in the vessel. This step is repeated additional one more time as described below.
[00175] Charge to the vessel 24% w/w sodium chloride solution (7.5 vol) at 20°C and stir for 10 min.. Separate the layers at 20°C and retain the organic phase in the vessel.
[00176] Heat the retained organic phase to 35°C and concentrate the mixture to 6.0 vol under reduced pressure maintaining 35°C.
[00177] Tetrahydrofuran charge, (15.0 vol, 13.2 wt) maintaining 35°C. Concentrate the mixture to 6.0 vol under reduced pressure maintaining 35°C.
[00178] Tetrahydrofuran charge, (15.0 vol, 13.2 wt) maintaining 35°C. Concentrate the mixture to 11.0 vol under reduced pressure maintaining 35°C.
[00179] Cool the mixture to -5°C. Load tert-butyl methyl ether, (10.0 vol, 7.4 wt) over 1 h maintaining -5°C. Stir the mixture at -5°C for 1.5 hours. Filter the solid on 1 to 2 pm filter cloth at -5°C. Wash the solid with pre-mixed tetrahydrofuran, (1.9 vol, 1.7 wt) and tert-butyl methyl ether, (3.1 vol, 1.9 wt) at -5°C as a displacement wash.
[00180] Wash the solid with tert-butyl methyl ether, (5.0 vol, 3.7 wt) at -5°C.
[00181] Dry the solid on the filter under a flow of nitrogen at 23°C.
[00182] Yield of compound P-1: 76-87%.
Step 3C: Preparation of compound 0-1
[00183] Charge purified water, (2.0 vol, 2.0 wt) followed by potassium phosphate, (3.3 eq, 1.54 wt), carefully portion-wise, maintaining <15°C, to vessel A. Charge toluene, (4.5 vol, 3.9 wt) to the vessel maintaining <15°C. As necessary, adjust the temperature to 10°C.
[00184] Charge P-1, (1.00 eq, 1.00 wt) to the vessel in two portions maintaining 10°C. Stir the reaction mixture at 10°C for 15 min..
[00185] Load F-3a, (1.1 eq, 0.64 wt) in 4 equal portions ensuring portions are spaced by 10 min. at 10°C.
[00186] Tetrabutylammonium iodide (TBAI) filler (0.20 eq, 0.16 wt). Heat the reaction mixture to 40°C. Stir the reaction mixture at 40°C for 30 h.
[00187] Charge pre-mixed 2-mercaptoacetic acid, (0.40 eq, 0.08 wt, 0.06 vol), and toluene, (0.5 vol, 0.4 wt) over 20 min. to Vessel A at 40°C. Line rinse with toluene, (0.5 vol, 0.4 wt) at 40°C. Adjust the temperature of the reaction mixture to 50°C. Stir the mixture at 50°C for 2.5 hours.
[00188] Adjust the temperature of Vessel A to 20°C. Charge purified water, (3.0 vol, 3.0 wt) maintaining 20°C. Stir the reaction mixture at 20°C for 15 min. and transfer to a new, clean HDPE container. Line/vessel rinse with toluene, (0.5 vol, 0.4 wt) at 20°C. Clarify (filter) the reaction mixture via a 1 pm filter at 20°C into clean Vessel A. Wash the vessel and the filter with toluene, (0.5 vol, 0.4 wt) at 20°C. Allow the layers to separate for 15 min. at 20°C, retaining the upper organic layer (organic layer 1).
[00189] Wash the aqueous layer with toluene, (2.5 vol, 2.2 wt) at 20°C for 15 min.. Allow the layers to separate for 15 min. at 20°C. Retain the upper organic layer (organic layer 2).
[00190] Combine the organic layer 1 and organic layer 2 and adjust the temperature to 20°C. Wash the combined organic layers with 10% w/w sodium chloride solution (5.0 vol) at 20°C for 15 min.. Allow the layers to settle for 15 min. at 20°C. Retain the upper organic layer.
[00191] Take the resulting solution of Ol into next reaction without isolation.
Step 3D: Preparation of compound Kl
[00192] Charge n-butanol, (2.4 wt, 3.0 vol) to vessel B and adjust to 5°C. Charge concentrated sulfuric acid, (1.1 wt, 5.0 eq, 0.6 vol) slowly to Vessel B maintaining <15°C. Line rinse with toluene, (0.4 wt, 0.5 vol) maintaining <15°C. Adjust the temperature of Vessel B to 25°C.
[00193] Heat the n-butanol/ sulfuric acid solution in Vessel B to 55°C. Charge the organic layer from Vessel A (from Step 3C) to the butanol/ sulfuric acid solution in Vessel B over 60 to 90 min. maintaining 55°C. Charge toluene, (1.3 wt, 1.5 vol) to Vessel A as a line rinse and transfer to Vessel B maintaining 55°C. Stir the contents of Vessel B at 55°C for 1.5 h.
[00194] Stir the mixture in Vessel B for 4.5 h at 55°C. Cool the contents of Vessel B to 20°C over 10 h. Filter the slurry over 1-2 pm filter cloth under nitrogen at 20°C. Wash the filter cake with pre-mixed toluene, (3.5 wt, 4.0 vol) and n-butanol, (1.0 vol, 0.8 wt) at 20°C. Wash the filter cake with toluene, (4.3 wt, 5.0 vol) at 20°C. Dry the solid at 30°C under vacuum.
[00195] Correct the output weight for assay. Expected 50-55% w/w.
[00196] Yield of compound K1: 89-92%.
Step 3E: Preparation of Mavorixafor Drug Substance
[00197] Charge Kl, (1.00 eq, 1.00 wt, corrected for HPLC assay) in vessel A followed by nitrogen-purged purified water, (2.0 wt, 2.0 vol) and if necessary, adjust the temperature to 20°C. Charge nitrogen-purged toluene, (12.0 wt, 14.0 vol) to the solution maintaining 20°C. Charge nitrogen-purged n-butanol, (0.8 wt, 1.0 vol) to the solution maintaining 20°C. Heat the biphasic mixture to 30°C. Charge nitrogen-purged 3.0 M aqueous sodium hydroxide solution (6.2 eq, 5.9 vol) maintaining 30°C. Check the pH (expected 12 to 13). Adjust the pH of the aqueous layer to pH 10.0 with nitrogen-purged 0.3 M sulfuric acid solution (expected up to 2.5 vol) maintaining 30°C. Stir the mixture at 30°C for 45 min..
[00198] Measure the pH to confirm the value is pH 10.0.
[00199] Allow the layers to settle at 30°C for 30 min. and separate the layers retaining the organic phase in the vessel, and discharge the aqueous layer into a separate container (container C).
[00200] Charge pre-mixed toluene, (4.1 wt, 4.7 vol) and n-butanol, (0.24 wt, 0.3 vol) to a separate vessel; heat the contents to 30°C and charge the aqueous layer from container C. As required adjust the temperature to 30°C and stir for 5 to 10 min. at 30°C. Allow the phases to separate for 10 to 15 min. at 30°C. Discharge the aqueous phase to waste and combine the organic phase to the organic phase in vessel A.
[00201] Charge nitrogen-purged purified water, (2.0 wt, 2.0 vol) to the organic layer maintaining the temperature at 30°C and stir for 5 to 10 min. at 30°C. Allow the phases to separate for 10 to 15 min. at 30°C. Discharge the aqueous phase to waste retaining the organic phase in the vessel. Heat the retained organic solution to 40°C. Concentrate the resulting organic phase to 7.0 vol by vacuum distillation at 40°C.
[00202] Charge nitrogen -purged toluene, (13.0 wt, 15.0 vol) to the mixture and concentrate the solution 7.0 vol by vacuum distillation at 40°C. This step is repeated additional one time as described below.
[00203] Charge nitrogen -purged toluene, (13.0 wt, 15.0 vol) to the mixture and concentrate the solution 7.0 vol by vacuum distillation at 40°C.
[00204] Charge nitrogen-purged toluene, (7.0 wt, 8.0 vol) to the mixture at 40°C, heat to 55°C and clarify the hot reaction mixture under nitrogen via a 1 pm filter.
[00205] Charge clarified nitrogen-purged toluene, (1.7 wt, 2.0 vol) to the mixture as a line and vessel rinse at 40°C. Concentrate the solution to 7.0 vol by vacuum distillation at 40°C. At the end of the distillation the product is expected to have precipitated. Heat the mixture to 63°C.
[00206] Adjust the temperature to 60.5°C. This batch will be referred to as the main batch.
[00207] Load seed material, (0.02 wt) to a new clean container. Charge clarified nitrogen-purged toluene, (0.09 wt, 0.10 vol) to this seed material and gently shake.
[00208] Seed the main batch with the slurry maintaining the temperature at 60.5 ± 2°C. Stir the reaction at the 60.5± 2°C for 1 hour.
[00209] Cool to 40°C for 2.5 h. Stir the reaction at 40°C for 1 hour.
[00210] Cool to 30°C over 2 h.. Stir the reaction at 30°C for 1 h.
[00211] Cool to 25°C 50 min. Stir the reaction at 25°C over 2 hours.
[00212] Cool to 2°C over 4 h. Stir the mixture for 12 hours at 2°C.
[00213] Filter the mixture at 2°C over 1 to 2 pm cloth. Wash the filter cake with clarified nitrogen-purged toluene, (2.0 vol, 1.7 wt) at 2°C. Dry the filter cake under vacuum and a flow of nitrogen for 1.5 h.
[00214] Dry the solid at 40°C under vacuum and a flow of nitrogen until drying specification is achieved.
[00215] Yield of the final compound mavorixafor: 72%.
[00216] When toluene is used as the recrystallization solvent, optionally with a dissolution aid such butanol or methanol, for maxorixa for recrystallization, advantages were found compared to using dichloromethane and isopropyl acetate. We have found that these solvents do not react with the API, and accordingly we believe that this change has caused the significant reduction of impurities A (imine), B (N-formyl) and C (acetamide) that we have observed.
[00217] In some embodiments, the mavorixafor composition included 7000, 6000, 5000, 4500, 4450, 4000, 3500, 3000, 2500, 2000, 1750, 1700, 1650, 1600, 1550, 1500, 1450, 1400, 1400, 1400, 1400 gold 50 ppm of toluene or less. In some embodiments, the mavorixafor composition comprises a detectable amount of toluene. In some embodiments, the mavorixafor composition comprises from a detectable amount of toluene to 1350 ppm of toluene.

////////

AS ON DEC2021 3,491,869 VIEWS ON BLOG WORLDREACH AVAILABLEFOR YOUR ADVERTISEMENT
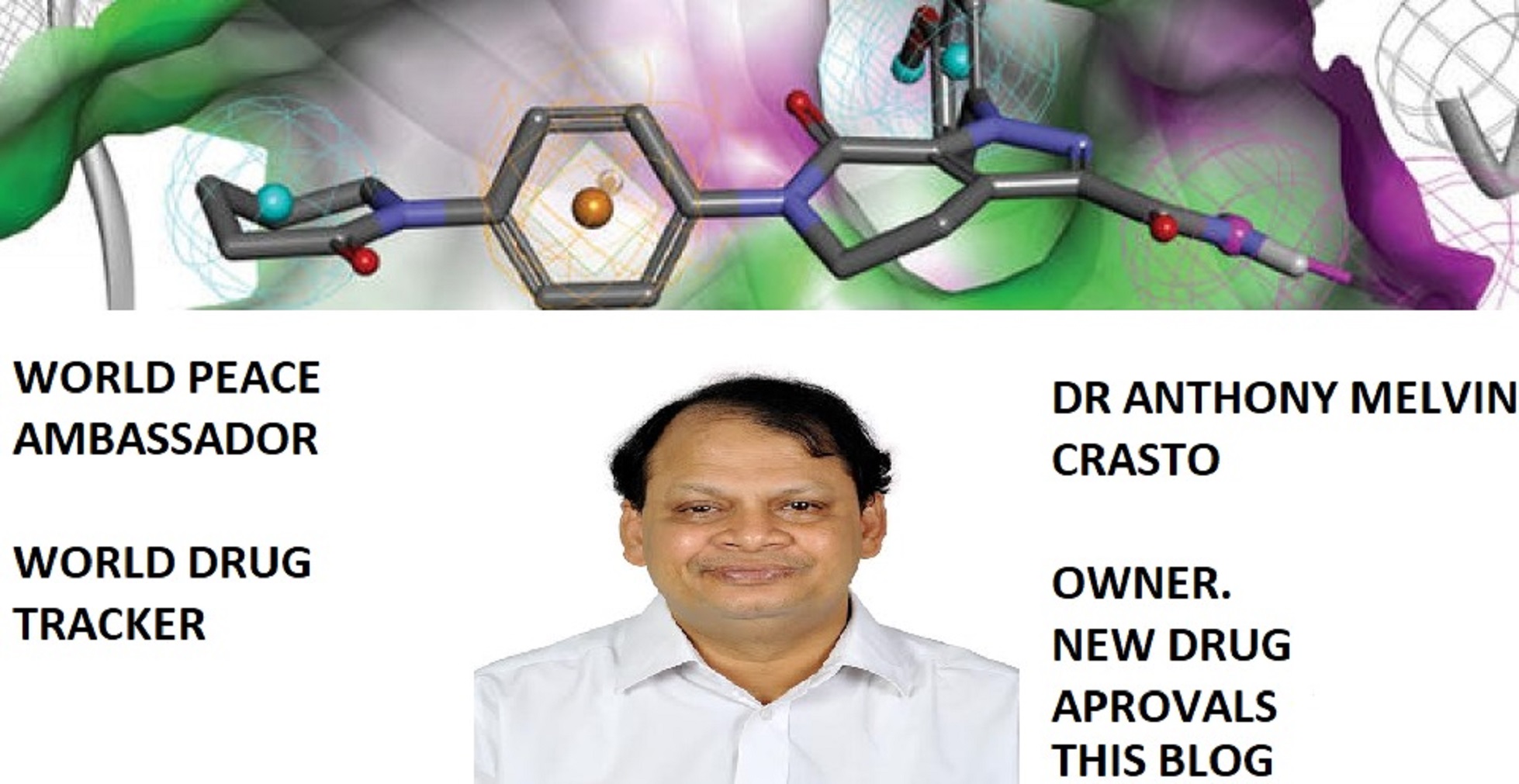
join me on Linkedin
Anthony Melvin Crasto Ph.D – India | LinkedIn
join me on Researchgate
RESEARCHGATE

join me on Facebook
Anthony Melvin Crasto Dr. | Facebook
join me on twitter
Anthony Melvin Crasto Dr. | twitter
+919321316780 call whatsaapp
EMAIL. amcrasto@amcrasto
Description | Mavorixafor (AMD-070) is a potent, selective and orally available CXCR4 antagonist, with an IC50 value of 13 nM against CXCR4 125I-SDF binding, and also inhibits the replication of T-tropic HIV-1 (NL4.3 strain) in MT-4 cells and PBMCs with an IC50 of 1 and 9 nM, respectively. |
---|---|
IC50 & Target[1] | 125I-SDF-CXCR413 nM (IC50)HIV-1 (NL4.3 strain)1 nM (IC50, in MT-4 cells)HIV-1 (NL4.3 strain)9 nM (IC50, in PBMCs)HIV-1 (NL4.3 strain)3 nM (IC90, in MT-4 cells)HIV-1 (NL4.3 strain)26 nM (IC90, in PBMCs) |
In Vitro | Mavorixafor (AMD-070) is a potent and orally available CXCR4 antagonist, with an IC50 value of 13 nM against CXCR4 125I-SDF binding, and also inhibits the replication of T-tropic HIV-1 (NL4.3 strain) in MT-4 cells and PBMCs with an IC50 of 1 and 9 nM, respectively. Mavorixafor (AMD-070) shows no effect on other chemokine receptors (CCR1, CCR2b, CCR4, CCR5, CXCR1, and CXCR2)[1]. Mavorixafor (AMD-070) (6.6 µM) significantly suppresses the anchorage-dependent growth, the migration and matrigel invasion of the B88-SDF-1 cells[2].MCE has not independently confirmed the accuracy of these methods. They are for reference only. |
In Vivo | Mavorixafor (AMD-070) (2 mg/kg, p.o.) significantly reduces the number of metastatic lung nodules in mice, and lowers the expression of human Alu DNA in mice, without body weight loss[2].MCE has not independently confirmed the accuracy of these methods. They are for reference only. |
Clinical Trial | NCT NumberSponsorConditionStart DatePhaseNCT00089466National Institute of Allergy and Infectious Diseases (NIAID)|AIDS Clinical Trials GroupHIV InfectionsNovember 2004Phase 1|Phase 2NCT02667886X4 PharmaceuticalsClear Cell Renal Cell CarcinomaJanuary 2016Phase 1|Phase 2NCT02823405X4 PharmaceuticalsMelanomaSeptember 15, 2016Phase 1NCT00361101Genzyme, a Sanofi Company|SanofiHIV Infections|X4 Tropic VirusOctober 2005Phase 1NCT03005327X4 PharmaceuticalsWHIM SyndromeDecember 2016Phase 2NCT04274738X4 PharmaceuticalsWaldenstrom´s MacroglobulinemiaApril 30, 2020Phase 1NCT04154488X4 PharmaceuticalsNeutropeniaOctober 16, 2020Phase 1NCT03995108X4 PharmaceuticalsWHIM SyndromeOctober 17, 2019Phase 3NCT05103917Abbisko Therapeutics Co, LtdTriple Negative Breast CancerJuly 21, 2021Phase 1|Phase 2NCT00063804National Institute of Allergy and Infectious Diseases (NIAID)|AIDS Clinical Trials GroupHIV Infections Phase 1NCT02923531X4 PharmaceuticalsClear Cell Renal Cell CarcinomaDecember 7, 2016Phase 1|Phase 2NCT02680782X4 Pharmaceuticals|CovanceHealthyJanuary 12, 2016Phase 1 |
REF
- [1]. Skerlj RT, et al. Discovery of novel small molecule orally bioavailable C-X-C chemokine receptor 4 antagonists that are potent inhibitors of T-tropic (X4) HIV-1 replication. J Med Chem. 2010 Apr 22;53(8):3376-88. [Content Brief][2]. Chow LN, et al. Impact of a CXCL12/CXCR4 Antagonist in Bleomycin (BLM) Induced Pulmonary Fibrosis and Carbon Tetrachloride (CCl4) Induced Hepatic Fibrosis in Mice. PLoS One. 2016 Mar 21;11(3):e0151765. [Content Brief][3]. Uchida D, et al. Effect of a novel orally bioavailable CXCR4 inhibitor, AMD070, on the metastasis of oral cancer cells. Oncol Rep. 2018 Jul;40(1):303-308. [Content Brief]
/////////////////////////////////////////////////////////////////////////////MAVORIXAFOR, AMD 070, PHASE 2

NEW DRUG APPROVALS
0NE TIME
$10.00
SC-52458, FORASARTAN

SC-52458, FORASARTAN
- Molecular FormulaC23H28N8
- Average mass416.522 Da
PHASE 2, PFIZER, HYPERTENSION
145216-43-9[RN]
5-[(3,5-Dibutyl-1H-1,2,4-triazol-1-yl)methyl]-2-[2-(1H-tetrazol-5-yl)phenyl]pyridine
5-[(3,5-dibutyl-1H-1,2,4-triazol-1-yl)methyl]-2-[2-(2H-1,2,3,4-tetrazol-5-yl)phenyl]pyridine
форасартан[Russian][INN], فوراسارتان[Arabic][INN], 福拉沙坦[Chinese][INN]
065F7WPT0B[DBID]
7415[DBID]
UNII-065F7WPT0B[DBID]
SC 52458[DBID]
Type-1 angiotensin II receptor
Forasartan, otherwise known as the compound SC-52458, is a nonpeptide angiotensin II receptor antagonist (ARB, AT1 receptor blocker).[2][3][4][5]
Forasartan, a specific angiotensin II antagonist, is used alone or with other antihypertensive agents to treat hypertension. Forasartan competes with angiotensin II for binding at the AT1 receptor subtype. As angiotensin II is a vasoconstrictor which also stimulates the synthesis and release of aldosterone, blockage of its effects results in a decreases in systemic vascular resistance.
Indications
Forasartan is indicated for the treatment of hypertension[6] and, similar to other ARBs, it protects the kidneys from kidney blood vessel damage caused by increased kidney blood pressure by blocking renin–angiotensin system activation.[7]
Administration
Forasartan is administered in the active oral form [6] which means that it must go through first pass metabolism in the liver. The dose administered ranges between 150 mg-200 mg daily.[6] Increasing to more than 200 mg daily does not offer significantly greater AT1 receptor inhibition.[6] Forasartan is absorbed quickly in the GI, and within an hour it becomes significantly biologically active.[6] Peak plasma concentrations of the drug are reached within one hour.[6]
Contraindications
Negative side effects of Forasartan are similar to other ARBs, and include hypotension and hyperkalemia.[8] There are no drug interactions identified with forasartan.[6]
Bioorganic & Medicinal Chemistry Letters (1994), 4(1), 99-104
PATENT
EP508445
https://worldwide.espacenet.com/patent/search/family/024755845/publication/EP0508445A1?q=EP508445A1
PATENT
WO1992018092
Example 2
2-[5-[(3,5-dibutyl-1H-1,2,4-triazol-1-yI)methyl]- 2-pyridinyl]benzoic acid
Step 1 : Preparation of 2-bromo-5-picoline .
A solution of 1500 mL (14 mol) of 48%
hydrobromic acid was cooled to 10 °C and 300 g (2.8 mol) of 2-amino-5-picoline (Aldrich) was added slowly. The
solution was maintained at or below 0 °C while 450 mL (8.8 mol) of bromime was added dropwise. After the bromine addition was complete, a solution of 500 g (7.3 mol) of sodium nitrite in 1000 mL of water was added slowly over 6 h. The reaction pH was adjusted by the careful addition of 1500 mL (56 mol) of 50% sodium hydroxide at such a rate that the temperature was maintained below 30 °C. The product precipitated from the nearly colorless reaction mixture; filtration gave 450 g (94%) of 2-bromo-5-picoline as a yellow powder: mp 38-40 °C; NMR 7.27 (s, 1H), 7.28 (s, 1H), 7.12 (br s, 1H).
Step 2 : Preparation of N-methyl-N-tertbutylbenzamide.
Under nitrogen, 96.7 g (1.1 mol) of N-methyl-N-tertbutylamine and 111 g (1.1 mol) of triethylamine was dissolved in 1050 mL of anhydrous tetrahydrofuran (THF).
The solution was cooled to 0 °C and treated with 140.6 σ (1.0 mol) of benzoyl chloride. The reaction was allowed to slowly warm to ambient temperature and stir overnight.
Filtration and subsequent concentration in vacuo of the filtrate gave the crude product which was purified by sublimation (65 °, 0.2 torr) to give 184 g (96%) of
colorless N-methyl-N-tertbutybenzamide: mp 80.5-82.0 °C; NMR (CDCI3) δ1.52 (s, 9H), 2.87 (s, 3H), 7.34-7.40 (m, 3H), 7.40-7.46 (m, 2H).
Step 3 : Preparation of 2-(N-methyl-N-tertbutylcarboxamido)phenyIboronic acid.
Under nitrogen, a solution of 50.0 g (262 mmol) of N-methyl-N-tertbutylbenzamide from step 2 and 44 ml (2S2 mmol) of tetramethylethylenediamine (TMEDA) in 3350 mL of anhydrous THF was cooled to -78 °C and slowly treated with 262 mmol of sec-butyllithium in cyclohexane. After 1 h at -78 °C, the reaction was treated with 45 mL (393 mmol) of trimethyl borate and allowed to slowly warm to ambient temperature overnight with stirring. The reaction was concentrated in vacuo; the residue was dissolved in IK sodium hydroxide and extracted with methylene chloride. The pH of the aqueous phase was adjusted to six with dilute hydrochloric acid and extracted with methylene chloride; the organic layer was dried (MgSO4) and concentrated in vacuo to give 55.7 g (90%) of a 80:20 mixture of syn/anti isomers of 2-(N-methyl-N-tertbutylcarboxamido)phenyIboronic acid as a pale yellow glass: NMR (CDCI3) δ 1.30 (s, syn C(CH3)3, 7.3H), 1.54 (s, anti 0(0.3)3, 1.7H), 2.81 (s, anti CH3, 0.6H), 2.94 (s, syn CH3, 2.4H), 7.29-7.46 (m, 3H), 7.95-8.01 (m, 1H).
step 4 : Preparation of N-methyl-N-tertbwtyl-2-(5-methyl-2-pyridinyl)benzamide.
Under nitrogen, 4.44 g (25.8 mmcl) cf 2-bromo-5-picoline from step 1 in 60 mL of toluene was treated with 6.75 g (29 mmol) of 2- (N-methyl-N- tertbutylcarboxamido)phenyIboronic acid from step 3, 1.0 g of tetrakis (triphenylphosphine)palladium zero, 26 mL of ethanol, and 29 mL of 2M sodium carbonate; this mixture was heated to reflux and vigorously stirred for 24 h. The reaction was partitioned between water and ether; the organic layer was separated, dried (MgSθ4), and
concentrated in vacuo. Purification by silica gel
chromatography (Waters Prep-500A) using ethyl
acetate/hexane (1:2) gave 6.51 g (90%) of N-methyl-N- tertbutyl-2-(5-methyl-2-pyridinyl)benzamide as an oil : NMR (CDCI3) δ 1.40 (s, 9H), 2.33 (s, 3H), 2.61 (s, 3H), 7.27- 7.33 (m, 1H), 7.35-7.41 (m, 2H), 7.47-7.51 (m, 2H), 7.60- 7.66 (m, 1H), 8.43 (br s, 1H).
Step 5 : Preparation of sodium 2-(5-methyl-2- pyridinyl)benzoate.
Under nitrogen, 6.5 g (23 mmol) of N-methyl-N- tertbutyl-2-(6-methyl-3-pyridinyl)benzamide from step 4 was treated with 65 mL of anhydrous trifluoroacetic acid (TFA) at reflux for 6 h. The reaction was concentrated in vacuo and the residue dissolved in water. The pH was adjusted to 10 with aqueous sodium hydroxide and lyophilized to give the sodium salt of 2- (5-methyl-2-pyridinyl)benzoic acid as a colorless solid: NMR [CDCI3/CF3CO2H (97:3)] δ 2.62 (s, 3H), 7.42-7.48 (m, 1H), 7.67-7.80 (m, 3H), 8.18-8.24 (m, 1H), 8.28 (dd, J=8 and 2 HZ, 1H), 7.67-7.80 (m, 3H), 8.18-8.24 (m, 1H), 8.28 (dd, J=8 and 2 Hz, 1H), 8.61 (s, 1H) ; MS (FAB) m/e (rel intensity) 214 (20), 196 (100); HRMS.
Calc’d for M+H: 214.0868. Found: 214.0846.
step 6 : Preparation of ethyl 2-(5-methyl-2-pyridinyl)benzoate.
Under nitrogen, the crude sodium salt from step 5 was suspended in 50 mL of chloroform and treated with 9 mL (103 mmol) of oxalyl chloride. The reaction was stirred for 72 h, filtered under nitrogen, and concentrated in vacuo; the residue was dissolved in absolute ethanol.
Concentration in vacuo gave 2.0 g (8 mmol) of ethyl 2-(5-methyl-2-pyridinyl)benzoate as a brown oil: NMR (CDCI3) δ 1.09 (t, J=7 Hz, 3H), 2.36 (s, 3H), 4.15 (q, J=7 Hz, 2H), 7.34 (d, J=8 Hz, 1H), 7.38-7.48 (m, 1H), 7.48-7.58 (m, 3H), 7.80 (d, J=8 Hz, 1H), 8.46 (s, 1H).
Step 7 : Preparation of ethyl 2-(5-bromomethyl-2-pyridinyl)benzoate.
Under nitrogen, the crude ethyl 2-(5-methyl-2-pyridinyl)benzoate from step 6 was treated with 1.7 g (9.5 mmol) of NBS and 160 mg (0.66 mmol) of benzoyl peroxide in 145 mL of anhydrous carbon tetrachloride at reflux for 2.5 h. The reaction was filtered under nitrogen and
concentrated in vacuo to give crude ethyl 2-(5-bromomethyl-2-pyridinyl)benzoate; no purification was attempted.
step 8 : Preparation of ethyl 2-[5-[(3,5-dibutyl-1H- 1 , 2 , 4-triazol-1 -yl )methy] 1 -2-pyridinyl ] benzoate .
Under nitrogen, 630 mg (3.5 mmol) of 3,5-dibutyl-1H-1,2,4-triazole from step 3 of Example 1 was added in small portions to 5.4 mmol of sodium hydride in 8 mL of DMF; stirring was continued until hydrogen evolution had ceased. The anion solution was cooled to 0 °C and treated with a solution of the crude ethyl 2-(5-bromomethyl-2-pyridinyl)benzoate from step 7 in 10 mL of DMF. The reaction was stirred at ambient temperature overnight, quench with 1 mL of absolute ethanol, and concentrated in vacuo; the resulting residue was redisolved in methylene chloride, filtered, and reconcentrated in vacuo to give crude ethyl 2-[5-[(3,5-dibutyl-1H-1,2,4-triazol-1-yl)methyl]-2-pyridinyl]benzoate.
step 9 : Preparation of 2- [5- [ (3, 5-dibutyl-1H-1 , 2, 4 -triazol-1-yl)methyl]-2-pyridinyllbenzoic acid.
A 1.0 g sample of the crude ethyl 2-[5-[(3,5-dibutyl-1H-1,2,4-triazol-1-yl)methyl]-2-pyridinyl]benzoate from step 8 in 10 mL of water was treated with 3 mL of 101 aqueous sodium hydroxide and stirred at ambient temperature overnight. The reaction mixture was washed with 30 mL of ether and the pH adjusted to six with dilute hydrochloric acid. Purification by reverse phase chromatography (Waters Deltaprep-3000) using isocratic acetonitrile/water (28:72) (0.05% TFA) gave 5 mg of 2-[5-[(3,5-dibutyl-1H-1,2,4-triazol-1-yl)methyl]-2-pyridinyl]benzoic acid: NMR (D2O + NaO3S(CH2)3 Si(CH3)3] δ 0.80 (t, J=7 Hz, 3H), 0.86 (t, J=7 Hz, 3H), 1.19-1.33 (m, 4H), 1.54-1.68 (m, 4H), 2.65 (t, J=7 Hz, 2H), 2.82 (t, _ϊ=7 Hz, 2H), 5.43 (s, 2H), 7.45-7.59 (m, 5H), 7.64 (dd, J=8 and 2 Hz, 1H), 8.37-8.45 (m, 1H); MS (FAB) m/e (rel intensity) 393 (80), 375 (30), 212 (40), 182 (100); HRMS. Calc’d for M+Li: 399.2373. Found:
399.2374.
Example 3
5-[2-[5-[(3,5-dibutyl-1H-1,2,4-triazol-1-yl)methyl]- 2-pyridinyl]phenyl]-1H-tetrazole
Step 1 : Preparation of 2-bromo-5-bromomethylpyridine.
A solution of 296.3 g (1.72 mol) of 2-bromo-5-picoline from step 1 of Example 2 in 6000 mL of carbon tetrachloride was treated with 306.5 g (1.72 mol) of N-bromosuccinimide (NBS) and 28.3 g (173 mmol) of
azobisisobutyronitrile (AIBN). The reaction was stirred at reflux under nitrogen for 3 h, filtered, and concentrated in vacuo providing 476 g of crude 2-bromo-5-bromomethylpyridine as a brownish yellow solid (NMR indicates that this material is only 60% monobromomethyl product): NMR (CDCI3 δ 4.42 (s, 2H), 7.48 (d, .J=9 Hz, 1H), 7.60 (dd, J=9 and 3 Hz, 1H), 8.37 (d, J=3 Hz, 1H).
Step 2: Preparation of 2-bromo-5-[(3.5-dibutyl-1H-1,2,4-triazol-1-yl)methyl]pyridine.
Under nitrogen, 3.15 g (17 mmol) of solid 3,5-dibutyl-1H-1,2,4-triazole from step 3 of Example 1 was added in small portions to 33 mmol of sodium hydride in 31 ml of dimethylformamide (DMF); stirring was continued until hydrogen evolution had ceased. The anion solution was cooled to 0 °C and treated with a solution of 7.9 g (19 mmol) of crude 2-bromo-5-bromomethylpyridine from step 1 in 10 ml of dry DMF. The reaction was allowed to warm to ambient temperature and stir overnight. Methanol (10 ml) was added to destroy any unreacted sodium hydride and the
DMF was removed in vacuo. The residue was dissolved in ethyl acetate, washed with water, and dried (MgSO4).
Silica gel chromatography (Waters Prep-500A) using ethyl acetate/hexane (60:40) gave 4.8 g (47%) of 2-bromo-5-[(3,5- dibutyl-1H-1,2,4-triazol-1-yl)methyl]pyridine as an oil: NMR (CDCI3) δ 0.88 (t, J=7 Hz, 1H), 0.92 (t, J=7 Hz, 1H), 1.27-1.44 (m, 4H), 1.59-1.76 (m, 4H), 2.60-2.71 (m, 4H), 5.18 (s, 2H), 7.35 (dd, J=8 and 3 Hz), 7.46 (d, J=8 Hz, 1H), 8.23 (d, .1=3 Hz, 1H).
Step 3: Preparation of 5-[2-[5-[(3,5-dibutyl-1H-1,2,4- triazol-1-yl)methyl]-2-pyridinyl]phenyl]-1H-tetrazole.
Under nitrogen, 1.03 g (2.9 mmol) of 2-bromo-5- [(3,5-dibutyl-1H-1,2,4-triazol-1-yl)methyl]pyridine from step 2 and 2.46 g (5.7 mmol) of 2-(N-triphenyImethyltetrazol-5-yl)phenyIboronic acid from step 5 of Example 1 were treated with 1.0 g (0.86 mmol) of tetrakis (triphenyl-phosphine)palladium zero, 15 mL of toluene, 10 mL of ethanol, and 6.3 mL of 2M aqueous sodium carbonate. The reaction mixture was heated to reflux and vigorously stirred overnight. The product was purified by reverse phase chromatography (Waters Deltaprep-3000) using acetonitrile/water (20-40:80-60) (0.05% TFA). The pure fractions (by analytical HPLC) were combined, the
acetonitrile removed in vacuo, the pH adjusted to four with dilute sodium hydroxide, and the resulting suspension extracted 4 times with ether. The extracts were combined, dried (MgSθ4), and concentrated in vacuo to give 340 mg (28%) of 5-[2-[5-[(3,5-dibutyl-1H-1,2,4-triazol-1-yl)methyl]-2-pyridinyl]phenyl-1H-tetrazole as a colorless solid: mp 139-141 °C; NMR (CD3OD) δ 0.90 (t, J=7 Hz, 3H), 0.93 (t, J=7 Hz, 3H), 1.29-1.44 (m, 4H), 1.58-1.75 (m, 4H), 2.65 (t, J=7 Hz, 2H), 2.81 (t, J=7 Hz, 2H), 5.40 (s, 2H), 7.47 (d, J=8 Hz, 1H), 7.61-7.77 (m, 5H), 8.33 (d, J=2 Hz, 1H); MS (FAB) m/e (rel intensity) 417 (100), 208 (30); HRMS. Calc’d for M+H: 417.2515. Found: 417.2527.
PATENT
WO2001076573
////////

AS ON DEC2021 3,491,869 VIEWS ON BLOG WORLDREACH AVAILABLEFOR YOUR ADVERTISEMENT
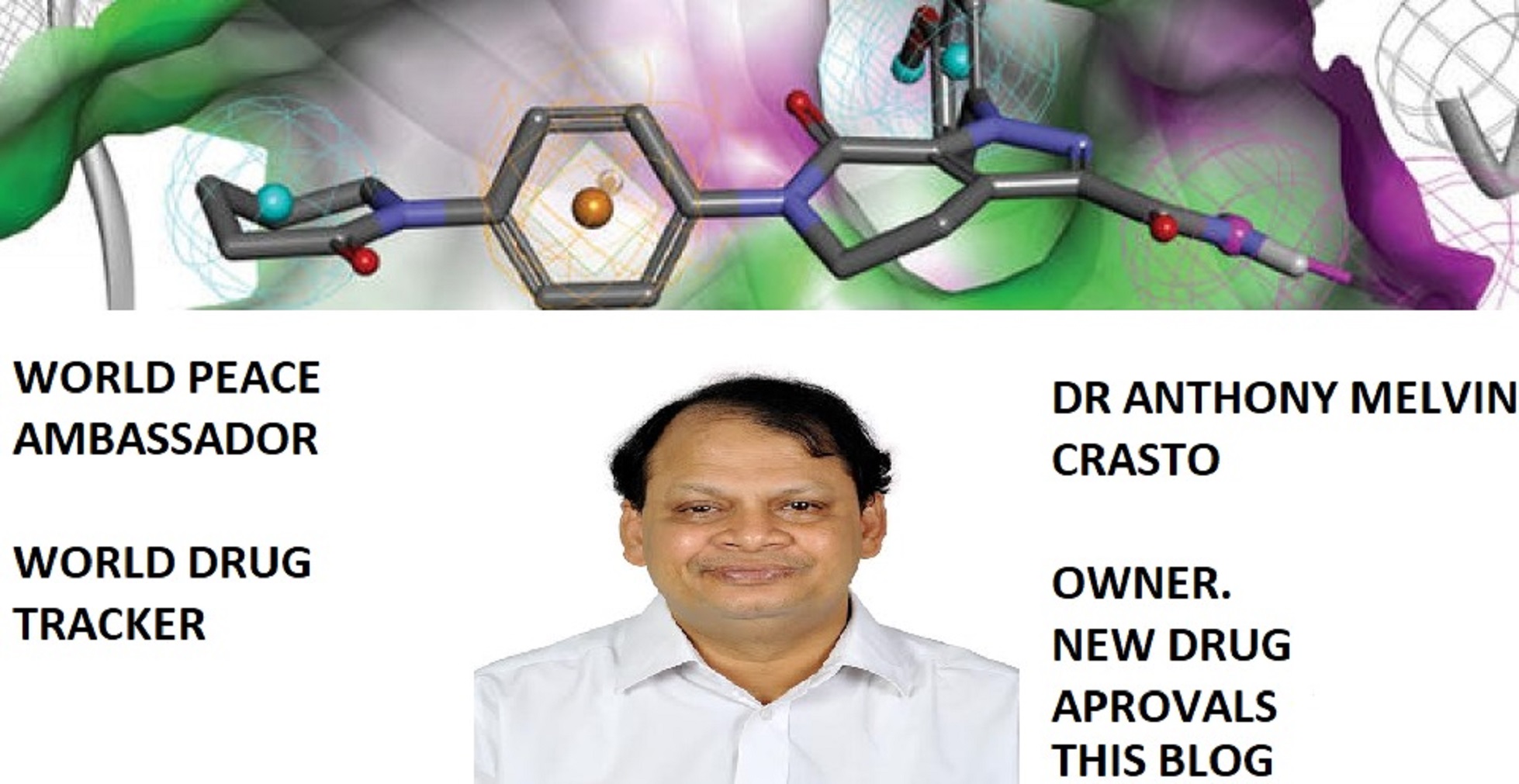
join me on Linkedin
Anthony Melvin Crasto Ph.D – India | LinkedIn
join me on Researchgate
RESEARCHGATE

join me on Facebook
Anthony Melvin Crasto Dr. | Facebook
join me on twitter
Anthony Melvin Crasto Dr. | twitter
+919321316780 call whatsaapp
EMAIL. amcrasto@amcrasto
/////////////////////////////////////////////////////////////////////////////
Pharmacology
The angiotensin II receptor, type 1
Angiotensin II binds to AT1 receptors, increases contraction of vascular smooth muscle, and stimulates aldosterone resulting in sodium reabsorption and increase in blood volume.[9] Smooth muscle contraction occurs due to increased calcium influx through the L-type calcium channels in smooth muscle cells during the plateau component, increasing the intracellular calcium and membrane potential which sustain depolarization and contraction.[10]
Effects
Forasartan is a competitive and reversible ARB that competes with the angiotensin II binding site on AT1[11] and relaxes vascular smooth muscle,[10] resulting in decreased blood pressure. Forasartan has a high affinity for the AT1 receptor (IC50=2.9 +/- 0.1nM).[12] In dogs, it was found to block the pressor response of Angiotensin II with maximal inhibition, 91%.[10] Forasartan administration selectively inhibits L-type calcium channels in the plateau component of the smooth muscle cells, favoring relaxation of the smooth muscle.[10] Forasartan also decreases heart rate by inhibiting the positive chronotropic effect of high frequency preganglionic stimuli.[13]
Scarce use
Even though experiments have been conducted on rabbits,[6] guinea pigs,[10] dogs [14] and humans,[6][13] forasartan is not a popular drug of choice for hypertension due to its short duration of action; forasartan is less effective than losartan.[6] Research demonstrates that forasartan is also significantly less potent than losartan.[6]
See also
References
- ^ Bräse, Stefan; Banert, Klaus (2010). Organic Azides: Syntheses and Applications. New York: Wiley. p. 38. ISBN 978-0-470-51998-1.
- ^ Knox C, Law V, Jewison T, Liu P, Ly S, Frolkis A, et al. (January 2011). “DrugBank 3.0: a comprehensive resource for ‘omics’ research on drugs”. Nucleic Acids Research. DrugBank. 39 (Database issue): D1035-41. doi:10.1093/nar/gkq1126. PMC 3013709. PMID 21059682.
- ^ Wishart DS, Knox C, Guo AC, Cheng D, Shrivastava S, Tzur D, et al. (January 2008). “DrugBank: a knowledgebase for drugs, drug actions and drug targets”. Nucleic Acids Research. 36 (Database issue): D901-6. doi:10.1093/nar/gkm958. PMC 2238889. PMID 18048412.
- ^ Wishart DS, Knox C, Guo AC, Shrivastava S, Hassanali M, Stothard P, et al. (January 2006). “DrugBank: a comprehensive resource for in silico drug discovery and exploration”. Nucleic Acids Research. 34 (Database issue): D668-72. doi:10.1093/nar/gkj067. PMC 1347430. PMID 16381955.
- ^ Olins GM, Corpus VM, Chen ST, McMahon EG, Palomo MA, McGraw DE, et al. (October 1993). “Pharmacology of SC-52458, an orally active, nonpeptide angiotensin AT1 receptor antagonist”. Journal of Cardiovascular Pharmacology. 22 (4): 617–25. doi:10.1097/00005344-199310000-00016. PMID 7505365. S2CID 93468.
- ^ Jump up to:a b c d e f g h i j k Hagmann M, Nussberger J, Naudin RB, Burns TS, Karim A, Waeber B, Brunner HR (April 1997). “SC-52458, an orally active angiotensin II-receptor antagonist: inhibition of blood pressure response to angiotensin II challenges and pharmacokinetics in normal volunteers”. Journal of Cardiovascular Pharmacology. 29 (4): 444–50. doi:10.1097/00005344-199704000-00003. PMID 9156352.
- ^ Naik P, Murumkar P, Giridhar R, Yadav MR (December 2010). “Angiotensin II receptor type 1 (AT1) selective nonpeptidic antagonists–a perspective”. Bioorganic & Medicinal Chemistry. 18 (24): 8418–56. doi:10.1016/j.bmc.2010.10.043. PMID 21071232.
- ^ Ram CV (August 2008). “Angiotensin receptor blockers: current status and future prospects”. The American Journal of Medicine. 121 (8): 656–63. doi:10.1016/j.amjmed.2008.02.038. PMID 18691475.
- ^ Higuchi S, Ohtsu H, Suzuki H, Shirai H, Frank GD, Eguchi S (April 2007). “Angiotensin II signal transduction through the AT1 receptor: novel insights into mechanisms and pathophysiology”. Clinical Science. 112 (8): 417–28. doi:10.1042/cs20060342. PMID 17346243.
- ^ Jump up to:a b c d e Usune S, Furukawa T (October 1996). “Effects of SC-52458, a new nonpeptide angiotensin II receptor antagonist, on increase in cytoplasmic Ca2+ concentrations and contraction induced by angiotensin II and K(+)-depolarization in guinea-pig taenia coli”. General Pharmacology. 27 (7): 1179–85. doi:10.1016/s0306-3623(96)00058-4. PMID 8981065.
- ^ Olins GM, Chen ST, McMahon EG, Palomo MA, Reitz DB (January 1995). “Elucidation of the insurmountable nature of an angiotensin receptor antagonist, SC-54629”. Molecular Pharmacology. 47 (1): 115–20. PMID 7838120.
- ^ Csajka C, Buclin T, Fattinger K, Brunner HR, Biollaz J (2002). “Population pharmacokinetic-pharmacodynamic modelling of angiotensin receptor blockade in healthy volunteers”. Clinical Pharmacokinetics. 41 (2): 137–52. doi:10.2165/00003088-200241020-00005. PMID 11888333. S2CID 13185772.
- ^ Jump up to:a b Kushiku K, Yamada H, Shibata K, Tokunaga R, Katsuragi T, Furukawa T (January 2001). “Upregulation of immunoreactive angiotensin II release and angiotensinogen mRNA expression by high-frequency preganglionic stimulation at the canine cardiac sympathetic ganglia”. Circulation Research. 88 (1): 110–6. doi:10.1161/01.res.88.1.110. PMID 11139482.
- ^ McMahon EG, Yang PC, Babler MA, Suleymanov OD, Palomo MA, Olins GM, Cook CS (June 1997). “Effects of SC-52458, an angiotensin AT1 receptor antagonist, in the dog”. American Journal of Hypertension. 10 (6): 671–7. doi:10.1016/s0895-7061(96)00500-6. PMID 9194514.
Clinical data | |
---|---|
Other names | SC-52458 |
Pregnancy category | Not assigned |
Routes of administration | Oral |
ATC code | C09CA (WHO) |
Legal status | |
Legal status | Development halted, never marketed[1] |
Pharmacokinetic data | |
Elimination half-life | 1–2 hours |
Identifiers | |
showIUPAC name | |
CAS Number | 145216-43-9 |
PubChem CID | 132706 |
DrugBank | DB01342 |
ChemSpider | 117146 |
UNII | 065F7WPT0B |
KEGG | D04243 |
ChEBI | CHEBI:141552 |
ChEMBL | ChEMBL315021 |
CompTox Dashboard (EPA) | DTXSID70162942 |
Chemical and physical data | |
Formula | C23H28N8 |
Molar mass | 416.533 g·mol−1 |
3D model (JSmol) | Interactive image |
showSMILES | |
showInChI |
////////SC-52458, FORASARTAN, форасартан , فوراسارتان , 福拉沙坦 , PHASE 2, PFIZER, HYPERTENSION
CCCCC1=NN(CC2=CN=C(C=C2)C2=CC=CC=C2C2=NNN=N2)C(CCCC)=N1

NEW DRUG APPROVALS
one time
$10.00
ZYIL 1, Usnoflast

- Usnoflast
- ZYIL1
- ZYIL-1
- 2455519-86-3
- usnoflast [INN]
403.5 g/mol, C21H29N3O3S
1-[(E)-2-[(2R)-1,2-dimethylpyrrolidin-2-yl]ethenyl]sulfonyl-3-(1,2,3,5,6,7-hexahydro-s-indacen-4-yl)urea
Cryopyrin-associated periodic syndromes
ZYIL-1 is an oral, small-molecule inhibitor of the NLRP3 inflammasome in phase II clinical development at Zydus (formerly known as Cadila Healthcare and Zydus Cadila) for the treatment of cryopyrin-associated periodic syndromes (familial cold autoinflammatory syndrome (FCAS), Muckle-Wells syndrome (MWS) and neonatal onset multi-systemic inflammatory disease (NOMID; also known as chronic infantile neurologic cutaneous articular syndrome (CINCA)).
https://clinicaltrials.gov/ct2/show/NCT05186051
Condition or disease | Intervention/treatment | Phase 2 |
---|---|---|
Cryopyrin Associated Periodic Syndrome |
ZYIL1 is expected to show benefit in patients with CAPS. The present study aims to determine the safety, tolerability, pharmacokinetics, and pharmacodynamics of ZYIL1 when administered to subjects with CAPS.This is a phase 2a, prospective, open-label study. Primary objective of the study is to determine safety and tolerability profile of twice daily oral administration of ZYIL1 administered for 7 days. The study will be conducted in 3 subjects having CAPS as per eligibility criteria. The study will be divided in three periods: Screening Period; Run-in Period and Study Period.
Zydus announces positive Phase 2 Proof-of-Concept of NLRP3 inhibitor, ZYIL1 in patients with Cryopyrin Associated Periodic Syndrome (CAPS)
First Phase 2 Proof-of-Concept (POC) study demonstrating rapid clinical improvement and remission within days when Cryopyrin Associated Periodic Syndrome (CAPS) patients with flare ups were treated with ZYIL1, a novel oral small molecule NLRP3 inhibitor
Phase 1 study in Healthy Human volunteers published in “Clinical Pharmacology in Drug Development” Journal of American College of Clinical Pharmacology
AHMEDABAD, India I September 07, 2022 I Zydus Lifesciences Ltd. (formerly known as Cadila Healthcare Ltd.), a discovery-driven, global lifesciences company today announced that it has achieved a positive Proof-of-Concept in its Phase 2 clinical study of ZYIL1, in patients with CAPS.
CAPS is a rare, life-long, auto-inflammatory condition, caused by NLRP3 activating mutations and is classified as an orphan disease. The chronic inflammation due to IL-1beta release in CAPS patients leads to urticaria-like rash, fever, arthralgia, and increased risk of amyloidosis. CAPS patients also experience multiple neurological complications like sensorineural hearing loss, migraine, headache, aseptic meningitis and myalgia. Bone deformities and neurological impairments have been reported in Neonatal Onset Multisystem Inflammatory Disease (NOMID), the most severe form of CAPS.
The Phase 2 trial conducted in Australia, evaluated the Safety, Tolerability, Pharmacokinetics and Pharmacodynamics of ZYIL1 in Subjects with Cryopyrin Associated Periodic Syndromes (CAPS) [ClinicalTrials.gov Identifier: NCT05186051]. ZYIL1 showed rapid oral absorption. ZYIL1 is extremely potent (IC50 in nanomolar range) in human whole blood and supressed inflammation caused by the NLRP3 inflammasome. Robust effect on disease biomarkers including CRP, Serum Amyloid A (SAA), IL-6, WBC, was also observed.
ZYIL1 was safe and well-tolerated and there were no Serious Adverse Events (SAE’s) observed in this Phase 2 trial. Liver and kidney function tests also did not show any abnormalities in this Phase 2 trial. CAPS patients with confirmed NLRP3 mutation suffering from CAPS-related flare up, when treated with ZYIL1 in Phase 2 Proof-of-Concept trial showed rapid clinical improvement as early as day 3 which sustained till the end of treatment.
Lauding the positive proof-of-concept results achieved in CAPS patients as a significant milestone, Mr. Pankaj R. Patel, Chairman, Zydus Lifesciences Ltd. said, “As an innovation driven organization, we have been focussed on making a meaningful difference in the lives of patients. This top-line result from the Phase 2 clinical trial has demonstrated for the first time that ZYIL1, an oral small molecule NLRP3 inhibitor is beneficial in treating chronic inflammation in CAPS patients. Zydus is now planning to conduct further pivotal clinical trials and is committed to develop ZYIL1 for patients living with CAPS and other chronic inflammatory diseases.”
Reference:
1. ClinicalTrials.gov Identifier: NCT04972188 A Phase I, Prospective, Open Label, Multiple Dose Study of ZYIL1 Administered Via Oral Route to Investigate The Safety, Tolerability, Pharmacokinetics And Pharmacodynamics In Healthy Adult Subjects
2. ClinicalTrials.gov Identifier: NCT04731324 A Phase 1, Prospective Open Label, Single
Dose, Single Arm Study of ZYIL1 Administered Via Oral Route to Investigate the Safety, Tolerability, Pharmacokinetics and Pharmacodynamics in Healthy Adult Human Subjects
3. ClinicalTrials.gov Identifier: NCT05186051 A Phase 2a, Prospective, Open-Label Study to Evaluate the Safety, Tolerability, Pharmacokinetics and Pharmacodynamics of ZYIL1 in Subjects With Cryopyrin Associated Periodic Syndromes (CAPS)
4. Safety, Tolerability, Pharmacokinetics and Pharmacodynamics of the Oral NLRP3 Inflammasome Inhibitor ZYIL1: First-in-human Phase 1 studies (Single Ascending Dose and Multiple Ascending Dose), Clinical Pharmacology in Drug Development, 2022. DOI: 10.1002/cpdd.1162
About Zydus
The Zydus Group with an overarching purpose of empowering people with freedom to live healthier and more fulfilled lives, is an innovative, global lifesciences company that discovers, develops, manufactures, and markets a broad range of healthcare therapies. The group employs over 23000 people worldwide and is driven by its mission to unlock new possibilities in life- sciences through quality healthcare solutions that impact lives. The group aspires to transform lives through path-breaking discoveries. For more details visit www.zyduslife.com
PATENT
Example-6
(R,E)-N-((1,2,3,5,6,7-hexahydro-s-indacen-4-yl)carbamoyl)-2-(1-methylpyrrolidin-2-yl)ethene-1-sulfonamide
To solution of Intermediate 3a (1 eq.) in DCM (2.5 mL) added TFA (1 eq.) at 0°C.The reaction was wanned to r.t. & stirred further for 3h. The reaction mixture was concentrated in vacuo & purified by prep. HPLC to give product. To a solution of this product (1 eq.) in MeOH (7.0 mL) at r.t. was added Solid NaHCO3 (1.2 eq.) & stirred for 5 min. Formaldehyde (37% solution) (5 eq.) was added at r.t. and stirred for 2 h. Thereafter reaction mixture was treated with NaBH4 (1.5 eq.) portion wise at 0°C then reaction mixture was allowed to warm to r.t. stirred overnight. The reaction mixture was purified by prep. HPLC to give pure product. Altemateviely, Example 6 was also be prepared as per the procedure described for synthesis of Intermediate-7b (Example 111) using Intermediate 9 and (R)-1-methylpyrrolidine-2-carbaldehyde, together with conventional techniques known to those skilled in the art of organic synthesis.
1H NMR (400 MHz, DMSO-d6): δ = 10.53 (brs, 1H), 7.97 (s, 1H), 6.92 (s, 1H), 6.84 (d, J = 15.2 Hz, 1H), 6.53 (dd, J = 7.6 Hz , J = 15.2 Hz, 1H), 3.13 – 3.04 (m, 1H), 3.05 – 2.92 (m, 1H), 2.80 (t, J = 7.2 Hz, 4H), 2.67 (t, J = 7.2 Hz, 4H), 2.33 – 2.28 (m, 1H), 2.26 (s, 3H), 2.05 – 1.91 (m, 5H), 1.79 – 1.72 (m, 2H), 1.59 – 1.54 (m, 1H); MS (ESI): m/z (%) = 390.17 (100%) (M+H)+, 388.07 (30%) (M-1).
PATENTs
WO2021171230
WO2021111351
WO2021048809, IN202227014064
WO2020148619, EP3911631
WO2019043610, IN202027008328
US2020140382, IN201927046556, WO2018225018
/////////

AS ON DEC2021 3,491,869 VIEWS ON BLOG WORLDREACH AVAILABLEFOR YOUR ADVERTISEMENT
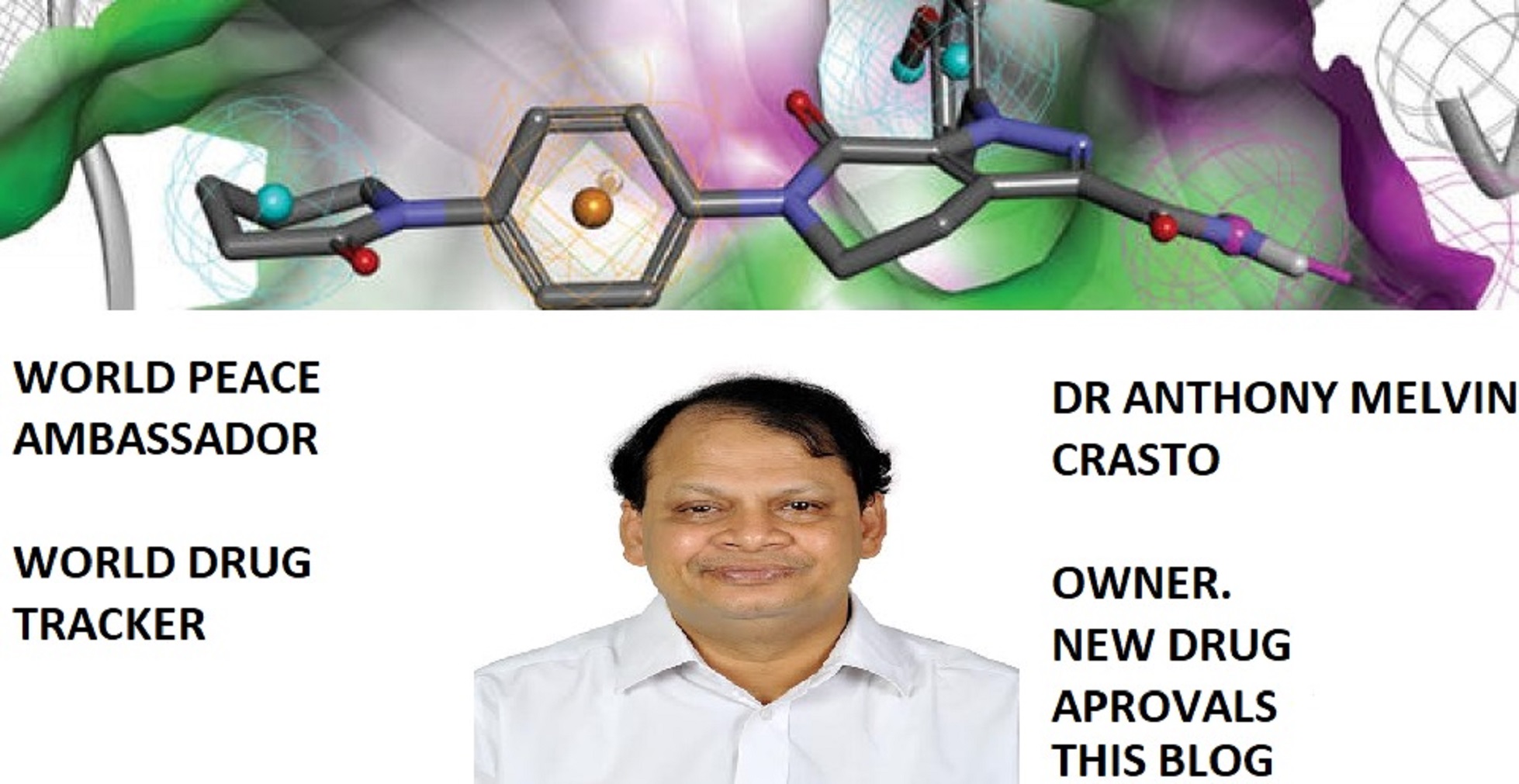
join me on Linkedin
Anthony Melvin Crasto Ph.D – India | LinkedIn
join me on Researchgate
RESEARCHGATE

join me on Facebook
Anthony Melvin Crasto Dr. | Facebook
join me on twitter
Anthony Melvin Crasto Dr. | twitter
+919321316780 call whatsaapp
EMAIL. amcrasto@amcrasto
/////////////////////////////////////////////////////////////////////////////
old………..
Zydus Cadila gets approval from DCGI for trial of novel molecule ZYIL1
Drug firm Zydus Cadila on Monday said it has received permission from Drugs Controller General of India (DCGI) to initiate phase-1 clinical trial of its novel molecule ZYIL1, indicated for use as an inhibitor for inflammation condition ‘NLRP3’.
In a regulatory filing, Zydus Cadila said “it has received permission to initiate the phase 1 clinical trial of ZYIL1, a novel oral small molecule NLRP3 inhibitor candidate. NLRP3 inflammasomes are involved in the inflammation process”.
This harmful inflammation within the body leads to the onset and development of various kinds of diseases, including Acute Respiratory Distress Syndrome (ARDS), auto-immune diseases, inflammatory diseases, cardiovascular diseases, metabolic disorders, Gastro-intestinal diseases (inflammatory bowel disease), renal diseases and CNS diseases, the company added.
Pankaj R Patel, Chairman, Cadila Healthcare said: “We will study the safety, tolerability, pharmacokinetics and pharmacodynamics of ZYIL1 in this phase I clinical trial in healthy human volunteers. We are committed to developing these pioneering novel treatments to the clinic for the patients in need.”
////////////ZYIL 1, PHASE 2, ZYDUS, ZYIL-1, CADILA

NEW DRUG APPROVALS
one time
$10.00
Camizestrant, AZD 9833


Camizestrant, AZD 9833
AZ 14066724
PHASE 2
CAS: 2222844-89-3
Chemical Formula: C24H28F4N6
Exact Mass: 476.2312
Molecular Weight: 476.5236
Elemental Analysis: C, 60.49; H, 5.92; F, 15.95; N, 17.64
N-(1-(3-fluoropropyl)azetidin-3-yl)-6-((6S,8R)-8-methyl-7-(2,2,2-trifluoroethyl)-6,7,8,9-tetrahydro-3H-pyrazolo[4,3-f]isoquinolin-6-yl)pyridin-3-amine
- AZ14066724
- AZD-9833
- AZD9833
- Camizestrant
- UNII-JUP57A8EPZ
- WHO 11592
- OriginatorAstraZeneca
- ClassAmines; Antineoplastics; Azetidines; Fluorinated hydrocarbons; Isoquinolines; Pyrazolones; Pyridines; Small molecules
- Mechanism of ActionSelective estrogen receptor degraders
- Phase IIIBreast cancer
- 13 Jun 2022AstraZeneca initiates a phase I drug-drug interaction trial of AZD 9833 Healthy postmenopausal female volunteers, in USA (NCT05438303)
- 10 Jun 2022AstraZeneca and Quotient Sciences complete the phase I QSC205863 trial in Breast cancer (In volunteers) in United Kingdom (PO, Liquid) (NCT05364255)
- 03 Jun 2022Safety, efficacy and pharmacokinetics data from the phase I SERENA 1 trial for Breast cancer presented at the 58th Annual Meeting of the American Society of Clinical Oncology (ASCO-2022)
- Mechanism:selective estrogen receptor degrader
- Area under investigation:estrogen receptor +ve breast cancer
- Date commenced phase:Q1 2019
- Estimated Filing Acceptance:
- CountryDateUS: EU: Japan: China:
AZD9833 is an orally available selective estrogen receptor degrader (SERD), with potential antineoplastic activity. Upon administration, SERD AZD9833 binds to the estrogen receptor (ER) and induces a conformational change that results in the degradation of the receptor. This prevents ER-mediated signaling and inhibits the growth and survival of ER-expressing cancer cells
Camizestrant is an orally available selective estrogen receptor degrader (SERD), with potential antineoplastic activity. Upon administration, camizestrant binds to the estrogen receptor (ER) and induces a conformational change that results in the degradation of the receptor. This prevents ER-mediated signaling and inhibits the growth and survival of ER-expressing cancer cells
SYN
https://www.thieme-connect.de/products/ejournals/abstract/10.1055/s-0040-1719368
Discovery of AZD9833, a Potent and Orally Bioavailable Selective Estrogen Receptor Degrader and Antagonist J. Med. Chem. 2020, 63, 14530–14559, DOI: 10.1021/acs.jmedchem.0c01163.

SYN
doi: 10.1021/acs.jmedchem.0c01163.

aReagents and Conditions: (a) n-BuLi, THF, −78 oC to 0 oC, 1 h, then 4 N HCl/dioxane, RT, 1 h, 60%; (b) alkyl triflate, DIPEA, 1,4-dioxane, 90 oC, 63-74% or isobutyrylaldehyde, Na(OAc)3BH, THF, 0 oC, 56%; (c) benzophenone imine, Pd2dba3, Rac-BINAP, NaOtBu, toluene, 90 oC, then 1 N aq. HCl, 71-85%; (d) nBuLi, THF, −78 oC to 0 oC, 1 h, then 4 N HCl/dioxane, RT, 4 h; e) NH2OH, NH2OH.HCl, EtOH, reflux. 84% over 2 steps; (f) alkyl triflate, DIPEA, 1,4-dioxane, 90 oC, 44-100% or 1-fluorocyclopropane-1- carboxylic acid, HATU, Et3N, DMF, RT, 61%, then BH3.THF, THF, 65 oC, 82%.

[α]26 D -147 (c 2.3, MeOH); 1H NMR (500 MHz, DMSO-d6, 27 °C) 1.08 (d, J = 6.6 Hz, 3H), 1.64 (dp, J = 25.0, 6.3 Hz, 2H), 2.45 (t, J = 6.9 Hz, 2H), 2.73(t, J = 6.8 Hz, 2H), 2.84 (dd, J = 17.1, 8.2 Hz, 1H), 2.96 (dt, J = 19.6, 9.8 Hz, 1H), 3.07 (dd, J = 17.2, 4.6 Hz, 1H), 3.49 (m, 1H), 3.50 – 3.58 (m, 1H), 3.58 – 3.66 (m, 2H), 3.92 (h, J = 6.5 Hz, 1H), 4.44 (dtd, J = 47.4, 6.1, 1.3 Hz, 2H), 4.93 (s, 1H), 6.23 (d, J = 6.9 Hz, 1H), 6.80 (d, J = 8.6 Hz, 1H), 6.83 (dt, J = 8.8, 2.0 Hz, 1H), 6.97 (d, J = 8.5 Hz, 1H), 7.22 (d, J = 8.6 Hz, 1H), 7.73 (d, J = 2.8 Hz, 1H), 8.05 (d, J = 1.3 Hz, 1H), 12.97 (s, 1H); 13C NMR (125 MHz, DMSO-d6, 27 °C) 16.2, 28.2 (d, J = 19.4 Hz), 30.1, 43.0, 47.3, 48.7 (q, J = 30.1 Hz), 54.8 (d, J = 5.6 Hz), 61.3 (2C), 67.1, 82.0 (d, J = 161.3 Hz), 107.5, 119.0, 122.4, 123.7, 126.1, 126.2 (q, J = 278.5 Hz), 126.4, 127.5, 131.7, 132.9, 138.5, 142.3, 150.0; 19F NMR (376 MHz, DMSO-d6, 27 °C) -218.1 (1F), -69.7 (3F); m/z (ES+), [M+H]+ = 477, HRMS (ESI) (MH+ ); calcd, 477.2408; found, 477.2390




/////////

AS ON DEC2021 3,491,869 VIEWS ON BLOG WORLDREACH AVAILABLEFOR YOUR ADVERTISEMENT
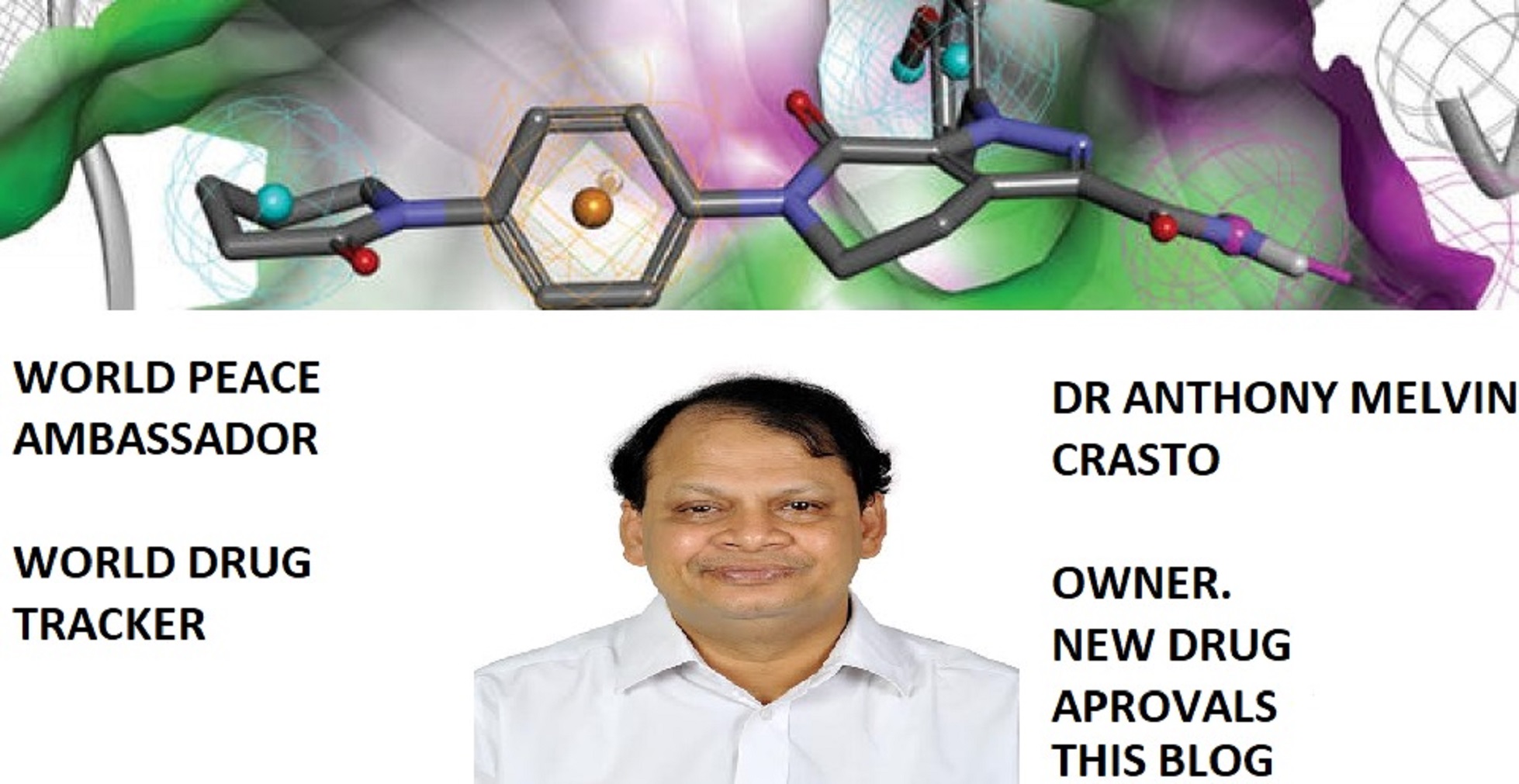
join me on Linkedin
Anthony Melvin Crasto Ph.D – India | LinkedIn
join me on Researchgate
RESEARCHGATE

join me on Facebook
Anthony Melvin Crasto Dr. | Facebook
join me on twitter
Anthony Melvin Crasto Dr. | twitter
+919321316780 call whatsaapp
EMAIL. amcrasto@amcrasto
/////////////////////////////////////////////////////////////////////////////
AZD9833 is selective oestrogen receptor degrader (SERD). It works by breaking down the site where oestrogen attaches to the cancer cell. This can help stop or slow the growth of hormone receptor breast cancer. Researchers think that AZD9833 with palbociclib might work better than anastrozole and palbociclib.
AZD9833 + palbociclib
The patients will receive AZD9833 (75 mg, PO, once daily) + palbociclib (PO, once daily, 125 mg for 21 consecutive days followed by 7 days off treatment) + anastrozole placebo (1 mg, PO, once daily)
SERENA-1: Study of AZD9833 Alone or in Combination in Women With Advanced Breast Cancer. (clinicaltrials.gov)…..https://veri.larvol.com/news/azd9833/drug
P1, N=305, Recruiting, AstraZeneca | Trial primary completion date: Dec 2022 –> Oct 2023
2 months ago
Trial primary completion date
|
HER-2 (Human epidermal growth factor receptor 2) • ER (Estrogen receptor) • PGR (Progesterone receptor)
|
HER-2 negative
Ibrance (palbociclib) • everolimus • Verzenio (abemaciclib) • capivasertib (AZD5363) • camizestrant (AZD9833)
Description | Camizestrant (AZD-9833) is a potent and orally active estrogen receptor (ER) antagonist. Camizestrant is used for the study of ER+ HER2-advanced breast cancer[1]. |
---|---|
IC50 & Target | IC50: estrogen receptor (ER)[1] |
In Vitro | Camizestrant is extracted from patent US20180111931A1, example 17[1].MCE has not independently confirmed the accuracy of these methods. They are for reference only. |
In Vivo | Camizestrant (oral administration; 0.2-50 mg/kg; 20 days) exhibits anti-tumour efficacy as a dose-dependent manner in human parental MCF7 mice xenograft[1]. Camizestrant (oral administration; 0.8-40 mg/kg; 30 days) decreases tumor growth as a dose-dependent manner. It gives almost complete tumour growth inhibition at the doses >10 mg/kg in mice[1]. MCE has not independently confirmed the accuracy of these methods. They are for reference only.Animal Model:Human ESR1 mutant breast cancer patient derived xenograft with CTC174 cells in female NSG mice[1]Dosage:0.8 mg/kg, 3 mg/kg, 10 mg/kg, 20 mg/kg, 40 mg/kgAdministration:Oral administration; 30 days; once dailyResult:Inhibited tumor growth in a dose-dependent manner. |
Clinical Trial | NCT NumberSponsorConditionStart DatePhaseNCT04711252AstraZenecaER-Positive HER2-Negative Breast CancerJanuary 28, 2021Phase 3NCT04964934AstraZenecaER-Positive HER2-Negative Breast CancerJune 30, 2021Phase 3NCT04214288AstraZenecaAdvanced ER-Positive HER2-Negative Breast CancerApril 22, 2020Phase 2NCT04588298AstraZenecaHER2-negative Breast CancerNovember 2, 2020Phase 2NCT04541433AstraZenecaER&addition; HER2- Advanced Breast CancerSeptember 29, 2020Phase 1NCT03616587AstraZenecaER&addition; HER2- Advanced Breast CancerOctober 11, 2018Phase 1NCT04546347AstraZeneca|Quotient SciencesHealthy VolunteersSeptember 17, 2020Phase 1NCT04818632AstraZenecaER&addition;, HER2-, Metastatic Breast CancerOctober 11, 2021Phase 1 |
////////////Camizestrant, AZD 9833, AZ 14066724, UNII-JUP57A8EPZ, WHO 11592, PHASE 2, ASTRA ZENECA, CANCER
C[C@@H]1CC2=C3C(NN=C3)=CC=C2[C@@H](C4=NC=C(NC5CN(CCCF)C5)C=C4)N1CC(F)(F)F

NEW DRUG APPROVALS
ONE TIME
$10.00
Rabeximod, ROB 803,
Rabeximod, ROB 803
C22H24ClN5O, 409.92
2-(9-chloro-2,3-dimethylindolo[3,2-b]quinoxalin-6-yl)-N-[2-(dimethylamino)ethyl]acetamide
CAS 872178-65-9UNII-J4D3K58W3Z, рабексимод , رابيكسيمود 雷贝莫德
6H-Indolo[2,3-b]quinoxaline-6-acetamide, 9-chloro-N-[2-(dimethylamino)ethyl]-2,3-dimethyl-
872178-65-9[RN]8866, J4D3K58W3Z
- OriginatorOxyPharma
- DeveloperCyxone; University of California
- ClassAcetamides; Anti-inflammatories; Disease-modifying antirheumatics; Heterocyclic compounds with 4 or more rings; Small molecules
- Mechanism of ActionCell differentiation modulators; Macrophage inhibitors
- Phase IICOVID 2019 infections; Rheumatoid arthritis
- 12 Oct 2021Cyxone terminates a phase-II trial in COVID-2019 infections in Slovakia (PO) (EudraCT2020-004571-41)
- 10 Aug 2021Cyxone completes a phase-II trial in COVID-2019 infections in Slovakia (PO) (EudraCT2020-004571-41)
- 23 Feb 2021Phase-II clinical trials in COVID-2019 infections in Slovakia (PO) (EudraCT2020-004571-41)
SYN
US 20050288296
https://patents.google.com/patent/US20050288296

AS ON DEC2021 3,491,869 VIEWS ON BLOG WORLDREACH AVAILABLEFOR YOUR ADVERTISEMENT
SYN
WO 2014140321
https://patents.google.com/patent/WO2014140321A1/en Example 29-chloro-7V- [2-(dimethylamino)ethyl] -2,3-dimethyl-6H-Indolo [2,3-6] quinoxaline-6- acetamide

This compound was prepared as described in PCT/SE2005/000718 (WO 2005/123741), cf. “Compound E” at page 12 of said WO pamphlet.SYNWO 2005/123741https://patentscope.wipo.int/search/en/detail.jsf?docId=WO2005123741
Compound E
9-Chloro-2,3-dimerthyl-6-(N,N-dimethylaminoethylamino-2-oxoethyl)-6H-indolo- [2,3-b]quinoxaline (R1=Cl, R2=CH3, X=CO, Y=NH-CH2-CH2-R3; R3=NR5R6;
R5=R6=CH3)
Yield: 58%; 1H-NMR δ: 8.29 (d, 1H), 8.23 (t, 1H), 7.98 (s, 1H), 7.82 (s, 1H), 7.71
(dd, 1H), 7.61 (d, 1H), 5.09 (s, 2H), 3,16 (q, 2H), 2.47 (s, 6H), 2.28 (t, 2H), 2,12
(s, 6H);
SYN

Rabeximod is an orally administered compound for treatment of moderate or severe active rheumatoid arthritis that is currently undergoing phase II clinical testing in eight European countries.
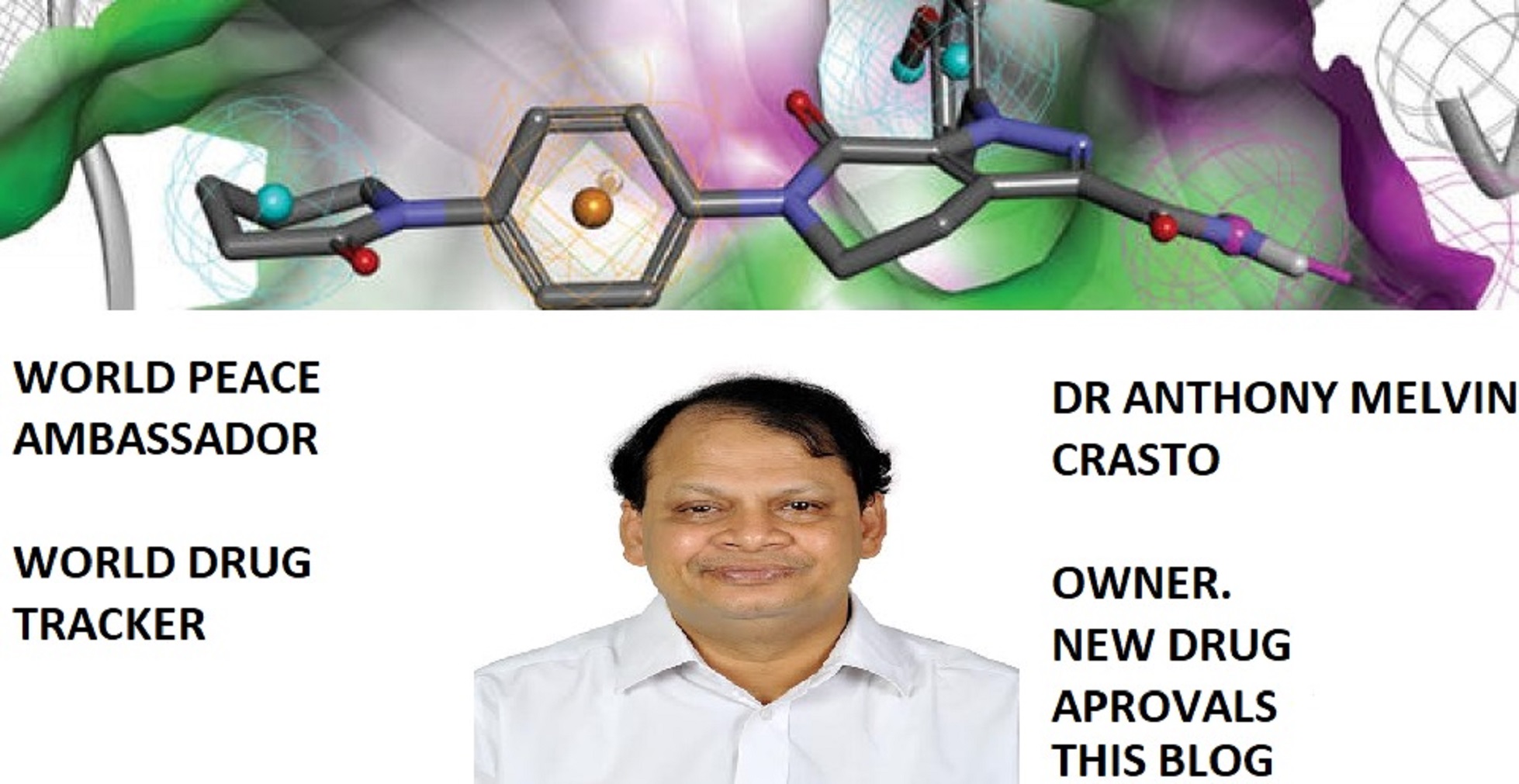
join me on Linkedin
Anthony Melvin Crasto Ph.D – India | LinkedIn
join me on Researchgate
RESEARCHGATE

join me on Facebook
Anthony Melvin Crasto Dr. | Facebook
join me on twitter
Anthony Melvin Crasto Dr. | twitter
+919321316780 call whatsaapp
EMAIL. amcrasto@gmail.com
////////////////////////////////////////
PATENT
The compound rabeximod has been described in European patent application publication EP1756111A1 later granted as EP1756111 B1. The preparation of rabex imod, as compound E, is specifically described in EP1756111A1 as a small-scale process without any description on how to develop a process that can be used for GMP and upscaled. Rabeximod was made in a 58% yield in a small-scale lab pro cess, but no parameters for scaling up have been disclosed.
The objective of the present invention is to provide a process that is suitable for large scale synthesis in good yield, with stable process parameters, and suitable for GMP production.
Experimental
The current process to manufacture Rabeximod involves several process steps as illustrated in below reaction scheme and as described in detail hereunder.

Manufacturing Process OXY001-01 Intermediate
Starting materials: 5-Chloroisatin (CIDO) and 4,5-Dimethyl-1 ,2-phenylenediamine (DAX)
Table 1: Overview Required Raw Materials and Quantities Step 1
Table 2: Raw Materials Specifications Step 1
Resulting Product (Intermediate): OXY001-01
Batch size: 13.03 kg of OXY001-01
Process description: 4,5-Dimethyl-1 ,2-phenylenediamine (1.1 equivalent) was added to acetic acid (4.7 volumes) in reactor (reactor was running under nitrogen at atmospheric pressure) and stirred up to 3 hours at moderate rate at +20 to +25 °C until clear dark brown solution was formed. 4, 5-Dimethyl-1 ,2-phenylenediamine so lution in acetic acid solution was transferred to intermediate feeding vessel. 5-chloro-isatin (1 .0 equivalent) was added to acetic acid (14.3 volumes) in reactor and stirred while jacket temperature of reactor was adjusted to approximately +150 °C to achieve a reflux temperature for active reflux of solvents. When reflux temperature was reached the 4, 5-Dimethyl-1 ,2-phenylenediamine solution in acetic acid was slowly added over 2-3 hours while distilling acetic acid (4.7 volumes) from the reaction mix ture. A fresh portion of acetic acid (4.7 volumes) was added to the reactor at about the same rate as distillation (4.7 volumes) occurred. After distillation the reaction mixture was stirred at reflux temperature for at least another 2 hours. The expected appearance of content in the reactor was a dark yellow to orange slurry. The reaction mixture was cooled to +65 to +70 °C and filtered using a Nutsche filter using Polyes ter filter cloth (27 pm) or similar as filter media. The filter cake was washed 3 times with fresh ethanol (3 x 4.2 volumes) and 1 time with water (1 x 4.2 volume). After washing the filter cake was dried at +40 to +45 °C for 12 hours and additionally in a vacuum tray dryer for 12 hours at +40 °C resulting in a yellow to orange/brown solid. An in-process control sample was taken and analysed for loss on drying (LOD). LOD should be < 2% (w/w). If the LOD is > 2%, the vacuum tray dryer step was repeated.
Theoretical yield: 18.62 kg
Yield: 70±5% (13.03±0.96kg)
Maximum volume: 216 L
Manufacturing Process OXY001-03 HCI Intermediate
CAC DMEN OXY001-03 HCI
Starting materials: Chloroacetyl chloride (CAC) and N,N-Dimethylethylene diamine (DMEN)
Table 3: Overview Required Raw Materials and Quantities Step 2
a) mol//mol of DMEN; b) kg/kg of DMEN; c) L/kg of DMEN
Table 4: Raw Materials Specifications Step 2
Resulting Product (Intermediate): OXY001-03 HCI
Batch size: 22.6 kg of OXY001 -03 HCI
Process description: Chloroacetyl chloride (1.03 equivalents) was dissolved in ethyl acetate (15 volumes) in reactor (reactor was running under nitrogen at atmos pheric pressure) at +20 °C. The solution was stirred and cooled down to +10 °C.
N,N-dimethylethylene diamine (1.00 equivalent) solution in ethyl acetate (1.0 volume) was slowly charged to the reactor when the temperature reached a range from +10 to +25 °C and at such a rate over 1-2 hours that the internal temperature did not exceed +25 °C. The slurry was stirred for 5 to 30 minutes at +20 to +25 °C and filtered using a Nutch filter using Polyamide filter cloth (25 pm) or similar as filter media. The product was washed 3 times on the filter with ethyl acetate (3 x 5 volumes) and dried on the filter for at least 16 hours and additionally in a vacuum tray dryer for 12 hours at +40 °C resulting in an off-white to beige solid.
Theoretical yield: 25.09 kg
Yield: 90±5% (22.6±1 .25 kg)
Maximum volume: 202 L
Manufacturing Process OXY001 Crude
– OXY001 Crude Starting materials: OXY001-01 and OXY001-03 HCI
Table 5: Overview Required Raw Materials and Quantities Step 3
Table 6: Raw/Intermediate Materials Specifications Step 3
Resulting Product: OXY001 Crude (crude rabeximod) Batch size: 11.38 kg of OXY001 Crude
Process description: OXY001-01 (1.0 equivalent) was dissolved in tetrahydrofuran (15.4 volumes) and 50% NaOH aqueous solution (8.0 equivalents in relation to OXY001 -01 ) in reactor (reactor was running under nitrogen at atmospheric pressure) and mixed at +55 to +60 °C up to approximately 1 hour until clear dark red solution was formed. Potassium iodide (0.81 equivalents) was added under vigorous stirring and mixed for 10 to 30 minutes at +55 to +60 °C. OXY001-03 HCI (2.0 equivalents) was added to the solution and mixed for at least 2 hours at +55 to +60 °C. Following completion of the reaction, the mixture was quenched with water (15.4 volumes) and tetrahydrofuran removed (15.4 volumes) by evaporation under reduced pressure. The slurry was cooled to +20 to +25 °C and stirred for 1 hour and filtered with a Nutch filter using Polyamide filter cloth (25 pm) or similar as filter media. Resulting cake was washed 3 times with water (3 x 5 volumes) until the pH of the filtrate was between 8-7 and dried on the filter at +40 to +45 °C for at least 12 hours by air suction and additionally in a vacuum tray dryer for 12 hours at +40 °C. Afterwards resulting ma terial was suspended in in tetrahydrofuran (25 volumes) at +45 to +50 °C for at least 1 hour. OXY001 Crude was isolated by filtration with a Nutch filter using Polyamide filter cloth (25 pm) or similar as filter media and washed 2 times on the filter with tetrahydrofuran (2 x 7 volumes). Resulting cake was dried on the filter at +40 to +45 °C for at least 12 hours and additionally in a vacuum tray dryer for 12 hours at +40 °C.
Theoretical yield: 18.96 kg
Yield: 60±5% (11 38±0.95 kg)
Maximum volume: 500 L
Purification of crude Rabeximod:
OXY001 crude (1 .0 equivalent) was dissolved in tetrahydrofuran (10 volumes), water (3 volume), and 2M HCI (1.4 volumes) mixture. The solution was clear filtered and heated to +50 °C. pH of mixture was adjusted to 10-12 by addition of 2M NaOH (1.3 volume). The formed slurry was cooled to +20 to +25 °C and diluted with water (12 volumes).
After stirring for at least 12 hours the slurry was filtered at +20 to +25 °C and washed on the filter with tetrahydrofuran:water (5:2) mixture (2×3 volumes). Rabeximod has a molecular weight of 409.92 g/mol and is isolated as a crystalline free base having a melting point of 259-261 °C.
Batch release results of batches used in Phase 2 and Phase 1 clinical studies are provided in Table 7.
Purity is equal to or above 98% as measured by HPLC.
Table 7: Batch release results of Rabeximod drug substance batches used in Phase 1 and phase 2 clinical studies
/////////////////Rabeximod, ROB 803, UNII-J4D3K58W3Z, рабексимод , رابيكسيمود 雷贝莫德 ,OXYPHARMA, PHASE 2, CYXONE
CC1=CC2=C(C=C1C)N=C3C(=N2)C4=C(N3CC(=O)NCCN(C)C)C=CC(=C4)Cl

NEW DRUG APPROVALS
ONE TIME
$10.00
AUPM 170, CA 170, PD-1-IN-1




(2S,3R)-2-(3-((S)-3-amino-1-(3-((R)-1-amino-2-hydroxyethyl)-1,2,4-oxadiazol-5-yl)-3-oxopropyl)ureido)-3-hydroxybutanoic acid
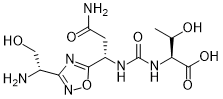


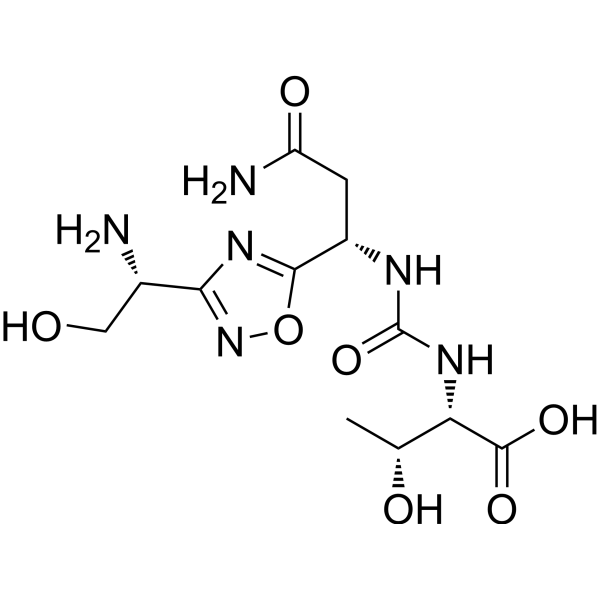
Molecular Weight (MW) | 360.33 |
---|---|
Formula | C12H20N6O7 |
CAS No. | 1673534-76-3 |
N-[[[(1S)-3-Amino-1-[3-[(1R)-1-amino-2-hydroxyethyl]-1,2,4-oxadiazol-5-yl]-3-oxopropyl]amino]carbonyl]-L-threonine
L-Threonine, N-[[[(1S)-3-amino-1-[3-[(1R)-1-amino-2-hydroxyethyl]-1,2,4-oxadiazol-5-yl]-3-oxopropyl]amino]carbonyl]-
AUPM 170, CA 170, AUPM-170, CA-170, PD-1-IN-1
Novel inhibitor of programmed cell dealth-1 (PD-1)
CA-170 (also known as AUPM170 or PD-1-IN-1) is a first-in-class, potent and orally available small molecule inhibitor of the immune checkpoint regulatory proteins PD-L1 (programmed cell death ligand-1), PD-L2 and VISTA (V-domain immunoglobulin (Ig) suppressor of T-cell activation (programmed death 1 homolog; PD-1H). CA-170 was discovered by Curis Inc. and has potential antineoplastic activities. CA-170 selectively targets PD-L1 and VISTA, both of which function as negative checkpoint regulators of immune activation. Curis is currently investigating CA-170 for the treatment of advanced solid tumours and lymphomas in patients in a Phase 1 trial (ClinicalTrials.gov Identifier: NCT02812875).
References: www.clinicaltrials.gov (NCT02812875); WO 2015033299 A1 20150312.
Aurigene Discovery Technologies Limited INNOVATOR
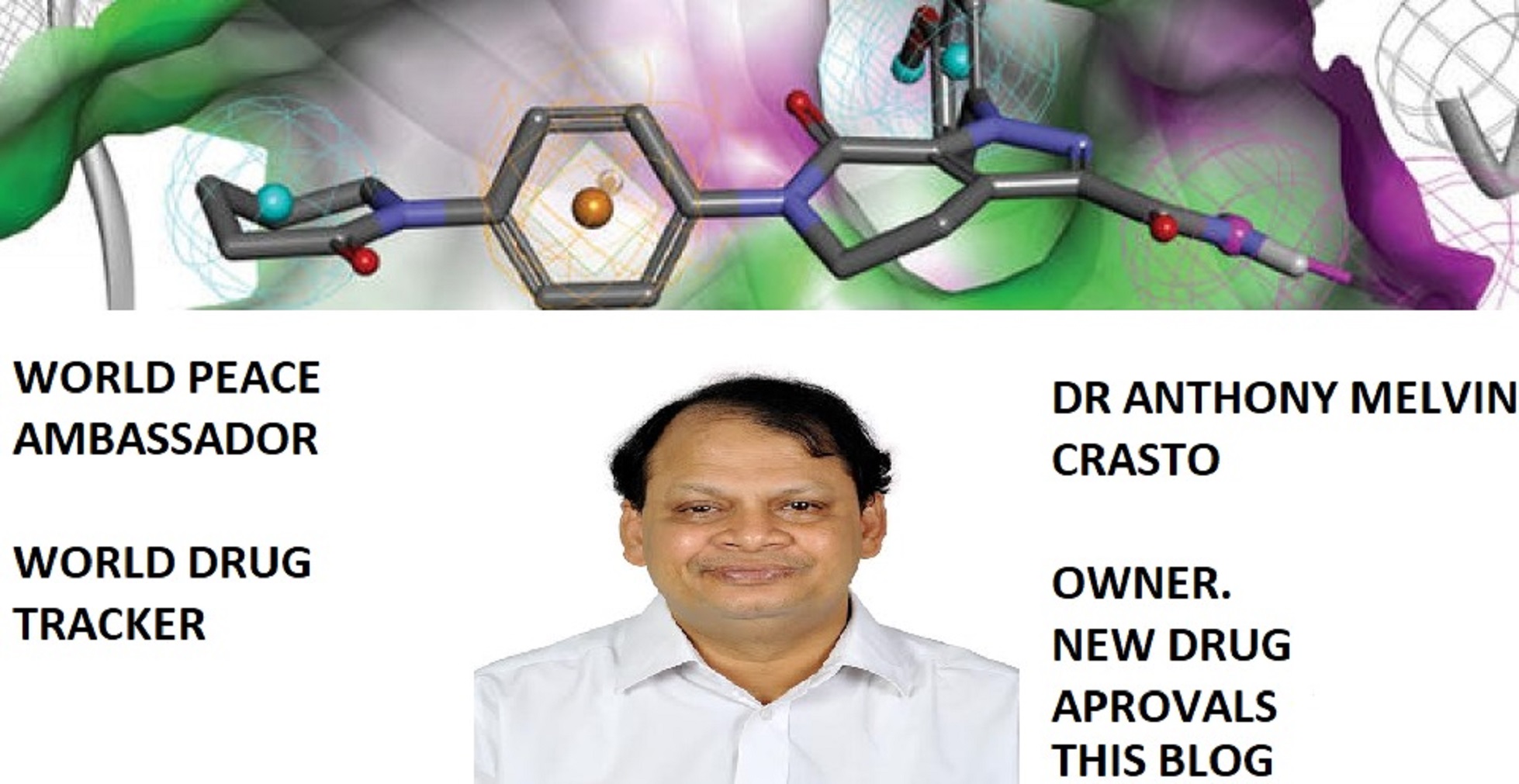
join me on Linkedin
Anthony Melvin Crasto Ph.D – India | LinkedIn
join me on Researchgate
RESEARCHGATE

join me on Facebook
Anthony Melvin Crasto Dr. | Facebook
join me on twitter
Anthony Melvin Crasto Dr. | twitter
+919321316780 call whatsaapp
EMAIL. amcrasto@amcrasto
/////////////////////////////////////////////////////////////////////////////////////////////////////
CURIS AND AURIGENE ANNOUNCE AMENDMENT OF COLLABORATION FOR THE DEVELOPMENT AND COMMERCIALIZATION OF CA-170
PRESS RELEASE
Curis and Aurigene Announce Amendment of Collaboration for the Development and Commercialization of CA-170
– Aurigene to fund and conduct a Phase 2b/3 randomized study of CA-170 in patients with non-squamous non-small cell lung cancer (nsNSCLC) –
– Aurigene to receive Asia rights for CA-170; Curis entitled to royalty payments in Asia –
LEXINGTON, Mass., February 5, 2020 /PRNewswire/ — Curis, Inc. (NASDAQ: CRIS), a biotechnology company focused on the development of innovative therapeutics for the treatment of cancer, today announced that it has entered into an amendment of its collaboration, license and option agreement with Aurigene Discovery Technologies, Ltd. (Aurigene). Under the terms of the amended agreement, Aurigene will fund and conduct a Phase 2b/3 randomized study evaluating CA-170, an orally available, dual
inhibitor of VISTA and PDL1, in combination with chemoradiation, in approximately 240 patients with nonsquamous
non-small cell lung cancer (nsNSCLC). In turn, Aurigene receives rights to develop and commercialize CA-170 in Asia, in addition to its existing rights in India and Russia, based on the terms of the original agreement. Curis retains U.S., E.U., and rest of world rights to CA-170, and is entitled to receive royalty payments on potential future sales of CA-170 in Asia.
In 2019, Aurigene presented clinical data from a Phase 2a basket study of CA-170 in patients with multiple tumor types, including those with nsNSCLC. In the study, CA-170 demonstrated promising signs of safety and efficacy in nsNSCLC patients compared to various anti-PD-1/PD-L1 antibodies.
“We are pleased to announce this amendment which leverages our partner Aurigene’s expertise and resources to support the clinical advancement of CA-170, as well as maintain our rights to CA-170 outside of Asia,” said James Dentzer, President and Chief Executive Officer of Curis. “Phase 2a data presented at the European Society for Medical Oncology (ESMO) conference last fall supported the potential for CA-170 to serve as a therapeutic option for patients with nsNSCLC. We look forward to working with our partner Aurigene to further explore this opportunity.”
“Despite recent advancements, patients with localized unresectable NSCLC struggle with high rates of recurrence and need for expensive intravenous biologics. The CA-170 data presented at ESMO 2019 from Aurigene’s Phase 2 ASIAD trial showed encouraging results in Clinical Benefit Rate and Prolonged PFS and support its potential to provide clinically meaningful benefit to Stage III and IVa nsNSCLC patients, in combination with chemoradiation and as oral maintenance” said Kumar Prabhash, MD, Professor of Medical Oncology at Tata Memorial Hospital, Mumbai, India.
Murali Ramachandra, PhD, Chief Executive Officer of Aurigene, commented, “Development of CA-170, with its unique dual inhibition of PD-L1 and VISTA, is the result of years of hard-work and commitment by many people, including the patients who participated in the trials, caregivers and physicians, along with the talented teams at Aurigene and Curis. We look forward to further developing CA-170 in nsNSCLC.”
About Curis, Inc.
Curis is a biotechnology company focused on the development of innovative therapeutics for the treatment of cancer, including fimepinostat, which is being investigated in combination with venetoclax in a Phase 1 clinical study in patients with DLBCL. In 2015, Curis entered into a collaboration with Aurigene in the areas of immuno-oncology and precision oncology. As part of this collaboration, Curis has exclusive licenses to oral small molecule antagonists of immune checkpoints including, the VISTA/PDL1 antagonist CA-170, and the TIM3/PDL1 antagonist CA-327, as well as the IRAK4 kinase inhibitor, CA- 4948. CA-4948 is currently undergoing testing in a Phase 1 trial in patients with non-Hodgkin lymphoma.
In addition, Curis is engaged in a collaboration with ImmuNext for development of CI-8993, a monoclonal anti-VISTA antibody. Curis is also party to a collaboration with Genentech, a member of the Roche Group, under which Genentech and Roche are commercializing Erivedge® for the treatment of advanced basal cell carcinoma. For more information, visit Curis’ website at http://www.curis.com.
About Aurigene
Aurigene is a development stage biotech company engaged in discovery and clinical development of novel and best-in-class therapies to treat cancer and inflammatory diseases and a wholly owned subsidiary of Dr. Reddy’s Laboratories Ltd. (BSE: 500124, NSE: DRREDDY, NYSE: RDY). Aurigene is focused on precision- oncology, oral immune checkpoint inhibitors, and the Th-17 pathway. Aurigene currently has several programs from its pipeline in clinical development. Aurigene’s ROR-gamma inverse agonist AUR-101 is currently in phase 2 clinical development under a US FDA IND. Additionally, Aurigene has multiple compounds at different stages of pre-clinical development. Aurigene has partnered with many large and mid-pharma companies in the United States and Europe and has 15 programs currently in clinical development. For more information, please visit Aurigene’s website at https://www.aurigene.com/
Curis with the option to exclusively license Aurigene’s orally-available small molecule antagonist of programmed death ligand-1 (PD-L1) in the immuno-oncology field
Addressing immune checkpoint pathways is a well validated strategy to treat human cancers and the ability to target PD-1/PD-L1 and other immune checkpoints with orally available small molecule drugs has the potential to be a distinct and major advancement for patients.
Through its collaboration with Aurigene, Curis is now engaged in the discovery and development of the first ever orally bioavailable, small molecule antagonists that target immune checkpoint receptor-ligand interactions, including PD-1/PD-L1 interactions. In the first half of 2016, Curis expects to file an IND application with the U.S. FDA to initiate clinical testing of CA-170, the first small molecule immune checkpoint antagonist targeting PD-L1 and VISTA. The multi-year collaboration with Aurigene is focused on generation of small molecule antagonists targeting additional checkpoint receptor-ligand interactions and Curis expects to advance additional drug candidates for clinical testing in the coming years. The next immuno-oncology program in the collaboration is currently targeting the immune checkpoints PD-L1 and TIM3.
In November 2015, preclinical data were reported. Data demonstrated tha the drug rescued and sustained activation of T cells functions in culture. CA-170 resulted in anti-tumor activity in multiple syngeneic tumor models including melanoma and colon cancer. Similar data were presented at the 2015 AACR-NCI-EORTC Molecular Targets and Cancer Therapeutics Conference in Boston, MA
By August 2015, preclinical data had been reported. Preliminary data demonstrated that in in vitro studies, small molecule PD-L1 antagonists induced effective T cell proliferation and IFN-gamma production by T cells that were specifically suppressed by PD-L1 in culture. The compounds were found to have effects similar to anti-PD1 antibodies in in vivo tumor models
(Oral Small Molecule PD-L1/VISTAAntagonist)
Certain human cancers express a ligand on their cell surface referred to as Programmed-death Ligand 1, or PD-L1, which binds to its cognate receptor, Programmed-death 1, or PD-1, present on the surface of the immune system’s T cells. Cell surface interactions between tumor cells and T cells through PD-L1/PD-1 molecules result in T cell inactivation and hence the inability of the body to mount an effective immune response against the tumor. It has been previously shown that modulation of the PD-1 mediated inhibition of T cells by either anti-PD1 antibodies or anti-PD-L1 antibodies can lead to activation of T cells that result in the observed anti-tumor effects in the tumor tissues. Therapeutic monoclonal antibodies targeting the PD-1/PD-L1 interactions have now been approved by the U.S. FDA for the treatment of certain cancers, and multiple therapeutic monoclonal antibodies targeting PD-1 or PD-L1 are currently in development.
In addition to PD-1/PD-L1 immune regulators, there are several other checkpoint molecules that are involved in the modulation of immune responses to tumor cells1. One such regulator is V-domain Ig suppressor of T-cell activation or VISTA that shares structural homology with PD-L1 and is also a potent suppressor of T cell functions. However, the expression of VISTA is different from that of PD-L1, and appears to be limited to the hematopoietic compartment in tissues such as spleen, lymph nodes and blood as well as in myeloid hematopoietic cells within the tumor microenvironment. Recent animal studies have demonstrated that combined targeting/ blockade of PD-1/PD-L1 interactions and VISTA result in improved anti-tumor responses in certain tumor models, highlighting their distinct and non-redundant functions in regulating the immune response to tumors2.
As part of the collaboration with Aurigene, in October 2015 Curis licensed a first-in-class oral, small molecule antagonist designated as CA-170 that selectively targets PD-L1 and VISTA, both of which function as negative checkpoint regulators of immune activation. CA-170 was selected from the broad PD-1 pathway antagonist program that the companies have been engaged in since the collaboration was established in January 2015. Preclinical data demonstrate that CA-170 can induce effective proliferation and IFN-γ (Interferon-gamma) production (a cytokine that is produced by activated T cells and is a marker of T cell activation) by T cells that are specifically suppressed by PD-L1 or VISTA in culture. In addition, CA-170 also appears to have anti-tumor effects similar to anti-PD-1 or anti-VISTA antibodies in multiple in vivo tumor models and appears to have a good in vivo safety profile. Curis expects to file an IND and initiate clinical testing of CA-170 in patients with advanced tumors during the first half of 2016.
Jan 21, 2015
Curis and Aurigene Announce Collaboration, License and Option Agreement to Discover, Develop and Commercialize Small Molecule Antagonists for Immuno-Oncology and Precision Oncology Targets
— Agreement Provides Curis with Option to Exclusively License Aurigene’s Antagonists for Immuno-Oncology, Including an Antagonist of PD-L1 and Selected Precision Oncology Targets, Including an IRAK4 Kinase Inhibitor —
— Investigational New Drug (IND) Application Filings for Both Initial Collaboration Programs Expected this Year —
— Curis to issue 17.1M shares of its Common Stock as Up-front Consideration —
— Management to Host Conference Call Today at 8:00 a.m. EST —
LEXINGTON, Mass. and BANGALORE, India, Jan. 21, 2015 (GLOBE NEWSWIRE) — Curis, Inc. (Nasdaq:CRIS), a biotechnology company focused on the development and commercialization of innovative drug candidates for the treatment of human cancers, and Aurigene Discovery Technologies Limited, a specialized, discovery stage biotechnology company developing novel therapies to treat cancer and inflammatory diseases, today announced that they have entered into an exclusive collaboration agreement focused on immuno-oncology and selected precision oncology targets. The collaboration provides for inclusion of multiple programs, with Curis having the option to exclusively license compounds once a development candidate is nominated within each respective program. The partnership draws from each company’s respective areas of expertise, with Aurigene having the responsibility for conducting all discovery and preclinical activities, including IND-enabling studies and providing Phase 1 clinical trial supply, and Curis having responsibility for all clinical development, regulatory and commercialization efforts worldwide, excluding India and Russia, for each program for which it exercises an option to obtain a license.
The first two programs under the collaboration are an orally-available small molecule antagonist of programmed death ligand-1 (PD-L1) in the immuno-oncology field and an orally-available small molecule inhibitor of Interleukin-1 receptor-associated kinase 4 (IRAK4) in the precision oncology field. Curis expects to exercise its option to obtain exclusive licenses to both programs and file IND applications for a development candidate from each in 2015.
“We are thrilled to partner with Aurigene in seeking to discover, develop and commercialize small molecule drug candidates generated from Aurigene’s novel technology and we believe that this collaboration represents a true transformation for Curis that positions the company for continued growth in the development and eventual commercialization of cancer drugs,” said Ali Fattaey, Ph.D., President and Chief Executive Officer of Curis. “The multi-year nature of our collaboration means that the parties have the potential to generate a steady pipeline of novel drug candidates in the coming years. Addressing immune checkpoint pathways is now a well validated strategy to treat human cancers and the ability to target PD-1/PD-L1 and other immune checkpoints with orally available small molecule drugs has the potential to be a distinct and major advancement for patients. Recent studies have also shown that alterations of the MYD88 gene lead to dysregulation of its downstream target IRAK4 in a number of hematologic malignancies, including Waldenström’s Macroglobulinemia and a subset of diffuse large B-cell lymphomas, making IRAK4 an attractive target for the treatment of these cancers. We look forward to advancing these programs into clinical development later this year.”
Dr. Fattaey continued, “Aurigene has a long and well-established track record of generating targeted small molecule drug candidates with bio-pharmaceutical collaborators and we have significantly expanded our drug development capabilities as we advance our proprietary drug candidates in currently ongoing clinical studies. We believe that we are well-positioned to advance compounds from this collaboration into clinical development.”
CSN Murthy, Chief Executive Officer of Aurigene, said, “We are excited to enter into this exclusive collaboration with Curis under which we intend to discover and develop a number of drug candidates from our chemistry innovations in the most exciting fields of cancer therapy. This unique collaboration is an opportunity for Aurigene to participate in advancing our discoveries into clinical development and beyond, and mutually align interests as provided for in our agreement. Our scientists at Aurigene have established a novel strategy to address immune checkpoint targets using small molecule chemical approaches, and have discovered a number of candidates that modulate these checkpoint pathways, including PD-1/PD-L1. We have established a large panel of preclinical tumor models in immunocompetent mice and can show significant in vivo anti-tumor activity using our small molecule PD-L1 antagonists. We are also in the late stages of selecting a candidate that is a potent and selective inhibitor of the IRAK4 kinase, demonstrating excellent in vivo activity in preclinical tumor models.”
In connection with the transaction, Curis has issued to Aurigene approximately 17.1 million shares of its common stock, or 19.9% of its outstanding common stock immediately prior to the transaction, in partial consideration for the rights granted to Curis under the collaboration agreement. The shares issued to Aurigene are subject to a lock-up agreement until January 18, 2017, with a portion of the shares being released from the lock-up in four equal bi-annual installments between now and that date.
The agreement provides that the parties will collaborate exclusively in immuno-oncology for an initial period of approximately two years, with the option for Curis to extend the broad immuno-oncology exclusivity.
In addition Curis has agreed to make payments to Aurigene as follows:
- for the first two programs: up to $52.5 million per program, including $42.5 million per program for approval and commercial milestones, plus specified approval milestone payments for additional indications, if any;
- for the third and fourth programs: up to $50 million per program, including $42.5 million per program for approval and commercial milestones, plus specified approval milestone payments for additional indications, if any; and
- for any program thereafter: up to $140.5 million per program, including $87.5 million per program in approval and commercial milestones, plus specified approval milestone payments for additional indications, if any.
Curis has agreed to pay Aurigene royalties on any net sales ranging from high single digits to 10% in territories where it successfully commercializes products and will also share in amounts that it receives from sublicensees depending upon the stage of development of the respective molecule.
About Immune Checkpoint Modulation and Programmed Death 1 Pathway
Modulation of immune checkpoint pathways has emerged as a highly promising therapeutic approach in a wide range of human cancers. Immune checkpoints are critical for the maintenance of self-tolerance as well as for the protection of tissues from excessive immune response generated during infections. However, cancer cells have the ability to modulate certain immune checkpoint pathways as a mechanism to evade the immune system. Certain immune checkpoint receptors or ligands are expressed by various cancer cells, targeting of which may be an effective strategy for generating anti-tumor activity. Some immune-checkpoint modulators, such as programmed death 1 (PD-1) protein, specifically regulate immune cell effector functions within tissues. One of the mechanisms by which tumor cells block anti-tumor immune responses in the tumor microenvironment is by upregulating ligands for PD-1, such as PD-L1. Hence, targeting of PD-1 and/or PD-L1 has been shown to lead to the generation of effective anti-tumor responses.
About Curis, Inc.
Curis is a biotechnology company focused on the development and commercialization of novel drug candidates for the treatment of human cancers. Curis’ pipeline of drug candidates includes CUDC-907, a dual HDAC and PI3K inhibitor, CUDC-427, a small molecule antagonist of IAP proteins, and Debio 0932, an oral HSP90 inhibitor. Curis is also engaged in a collaboration with Genentech, a member of the Roche Group, under which Genentech and Roche are developing and commercializing Erivedge®, the first and only FDA-approved medicine for the treatment of advanced basal cell carcinoma. For more information, visit Curis’ website at www.curis.com.
About Aurigene
Aurigene is a specialized, discovery stage biotechnology company, developing novel and best-in-class therapies to treat cancer and inflammatory diseases. Aurigene’s Programmed Death pathway program is the first of several immune checkpoint programs that are at different stages of discovery and preclinical development. Aurigene has partnered with several large- and mid-pharma companies in the United States and Europe and has delivered multiple clinical compounds through these partnerships. With over 500 scientists, Aurigene has collaborated with 6 of the top 10 pharma companies. Aurigene is an independent, wholly owned subsidiary of Dr. Reddy’s Laboratories Ltd. (NYSE:RDY). For more information, please visit Aurigene’s website at http://aurigene.com/.
POSTER



WO2011161699, WO2012/168944, WO2013144704 and WO2013132317 report peptides or peptidomimetic compounds which are capable of suppressing and/or inhibiting the programmed cell death 1 (PD1) signaling pathway.
PATENT

Inventors
- SASIKUMAR, Pottayil Govindan Nair
- RAMACHANDRA, Muralidhara
- NAREMADDEPALLI, Seetharamaiah Setty Sudarshan
Priority Data
4011/CHE/2013 | 06.09.2013 | IN |
Example 4: Synthesis of Co

The compound was synthesised using similar procedure as depicted in Example 2 for synthesising compound 2 using
instead of H-Ser(‘Bu)-0’Bu (in synthesis of compound 2b) to yield 0.35 g crude material of the title compound. The crude solid material was purified using preparative HPLC described under experimental conditions. LCMS: 361.2 (M+H)+, HPLC: tR = 12.19 min.
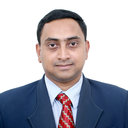
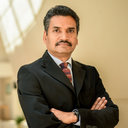
REFERENCES
US20150073024
WO2011161699A2 | 27 Jun 2011 | 29 Dec 2011 | Aurigene Discovery Technologies Limited | Immunosuppression modulating compounds |
WO2012168944A1 | 21 Dec 2011 | 13 Dec 2012 | Aurigene Discovery Technologies Limited | Therapeutic compounds for immunomodulation |
WO2013132317A1 | 4 Mar 2013 | 12 Sep 2013 | Aurigene Discovery Technologies Limited | Peptidomimetic compounds as immunomodulators |
WO2013144704A1 | 28 Mar 2013 | 3 Oct 2013 | Aurigene Discovery Technologies Limited | Immunomodulating cyclic compounds from the bc loop of human pd1 |
http://www.curis.com/pipeline/immuno-oncology/pd-l1-antagonist
http://www.curis.com/images/stories/pdfs/posters/Aurigene_PD-L1_VISTA_AACR-NCI-EORTC_2015.pdf
References:
1) https://bmcimmunol.biomedcentral.com/articles/10.1186/s12865-021-00446-4
2) https://www.nature.com/articles/s42003-021-02191-1
3) https://www.esmoopen.com/article/S2059-7029(20)30108-3/fulltext
4) https://www.mdpi.com/1420-3049/24/15/2804
////////Curis, Aurigene, AUPM 170, CA 170, AUPM-170, CA-170, PD-L1, VISTA antagonist, PD-1-IN-1, phase 2, CANCER
N[C@@H](CO)c1nc(on1)[C@@H](NC(=O)N[C@H](C(=O)O)[C@@H](C)O)CC(N)=O

NEW DRUG APPROVALS
ONE TIME
$9.00
AUR 101
AUR 101
AUR101-201
ANTIINNFLAMATORY
AUR-101, a ROR gamma inverse agonist for autoimmune disorders like psoriasis
AUR-101 is an ROR-gammaT inverse agonist in phase II clinical development at Aurigene for the treatment of patients with moderate-to-severe chronic plaque-type psoriasis.
- DrugsAUR 101 (Primary)
- IndicationsPlaque psoriasis
- FocusAdverse reactions; First in man
- AcronymsINDUS
- SponsorsAurigene Discovery Technologies
- OriginatorAurigene Discovery Technologies
- ClassAntipsoriatics; Small molecules
- Mechanism of ActionNuclear receptor subfamily 1 group F member 3 inverse agonists
- Phase IIPsoriasis
- 28 Aug 2021No recent reports of development identified for phase-I development in Psoriasis(In volunteers) in Australia (PO, Tablet)
- 23 Apr 2021Aurigene Discovery Technologies plans a phase II INDUS-3 trial for Psoriasis in USA (PO) in May 2021 (NCT04855721)
- 15 Apr 2021Aurigene Discovery Technologies completes a phase II trial in Psoriasis in India (PO) (NCT04207801)
- CDSCO
- https://www.cdsco.gov.in/opencms/resources/UploadCDSCOWeb/2018/UploadCTApprovals/Aurigene20.pdf
- NCT04207801
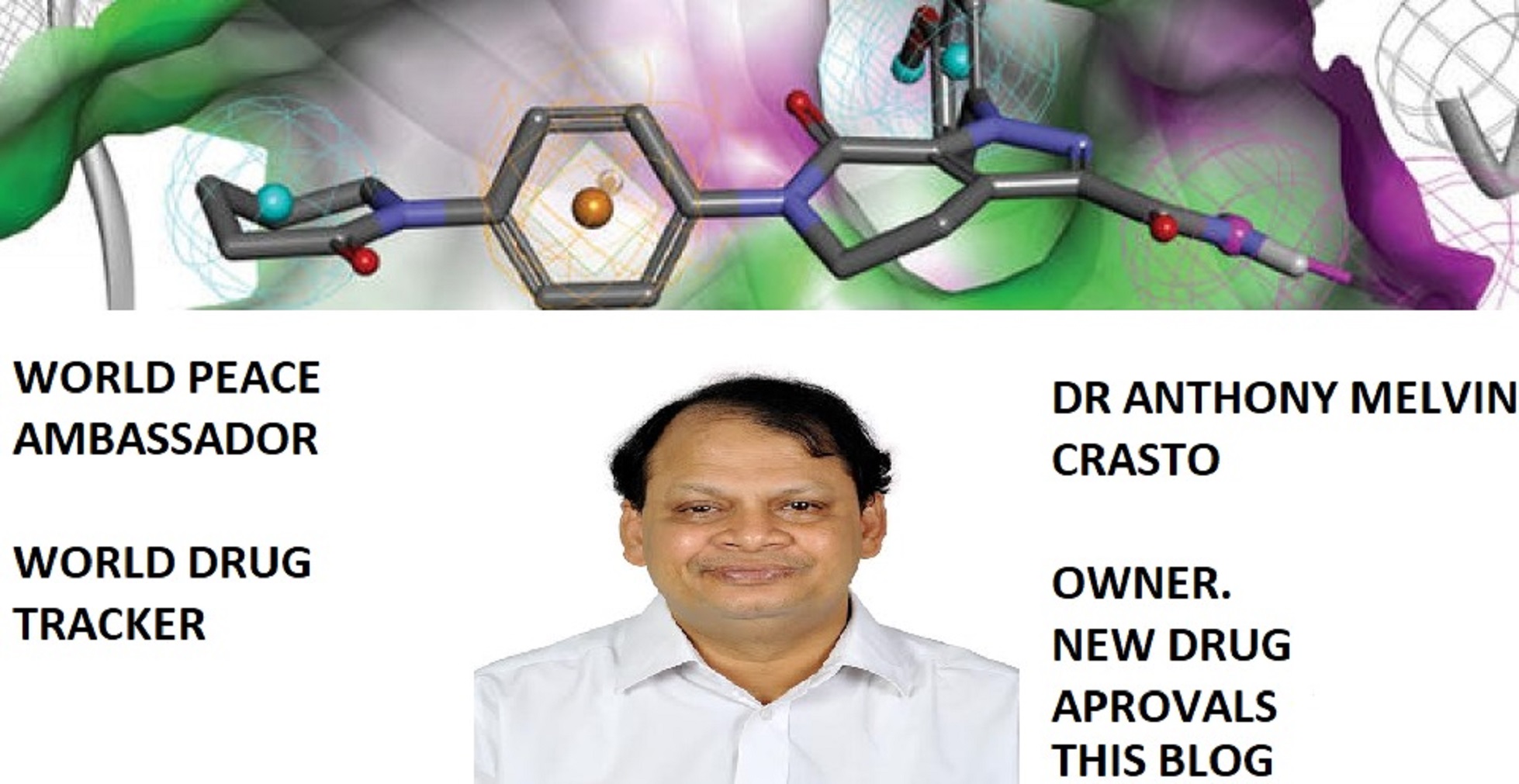
join me on Linkedin
Anthony Melvin Crasto Ph.D – India | LinkedIn
join me on Researchgate
RESEARCHGATE

join me on Facebook
Anthony Melvin Crasto Dr. | Facebook
join me on twitter
Anthony Melvin Crasto Dr. | twitter
+919321316780 call whatsaapp
EMAIL. amcrasto@amcrasto
/////////////////////////////////////////////////////////////////////////////////////////////////////
AURIGENE ANNOUNCES FIRST PATIENT DOSED WITH AUR101 IN PHASE II STUDY IN PATIENTS WITH MODERATE TO SEVERE PSORIASIS
PRESS RELEASE
Aurigene Announces First Patient Dosed with AUR101 in Phase II Study in Patients with Moderate to Severe Psoriasis
Bangalore, February 17, 2020 — Aurigene, a development stage biotechnology company, today announced dose administration for the first patient in INDUS-2, a Phase II double blind placebo-controlled three-arm study of AUR101 in patients with moderate to severe psoriasis. AUR101 is an oral small molecule inverse agonist of RORγ and has shown desirable pharmacodynamic modulation of IL-17 and acceptable safety in a completed Phase I human study conducted in Australia.
“The initiation of this Phase II study under a US FDA IND represents a significant milestone for Aurigene, as it marks the first program which Aurigene has led from the bench side to the clinic all by itself,” said Murali Ramachandra, PhD, Chief Executive Officer of Aurigene. “We look forward to producing important clinical data by the end of 2020 to guide our future development plans and demonstrating Aurigene’s unique expertise in conducting Proof-of-Concept studies in a quality and fast-paced manner.”
About AUR101-201 and the Phase II Study of AUR101 in Patients with Moderate to Severe Psoriasis
The purpose of the Phase II multi-center, blinded, placebo-controlled, three-arm study is to evaluate the clinical activity of AUR101 in patients with moderate to severe psoriasis. In two of the arms, AUR101 will be administered twice daily, at 400 mg PO BID and 600 mg PO BID, for 12 weeks. Patients in the third arm will receive matched blinded placebo in a double dummy fashion. The trial is listed at clinicaltrials.gov with identifier NCT04207801.
About Aurigene
Aurigene is a development stage biotech company engaged in discovery and clinical development of novel and best-in-class therapies to treat cancer and inflammatory diseases and a wholly owned subsidiary of Dr. Reddy’s Laboratories Ltd. (BSE: 500124, NSE: DRREDDY,NYSE: RDY). Aurigene is focused on precision- oncology, oral immune checkpoint inhibitors, and the Th-17 pathway. Aurigene currently has several programs from its pipeline in clinical development. Aurigene has also submitted an IND to DCGI, India for a Phase IIb/III trial of CA-170, a dual inhibitor of PD-L1 and VISTA, in non-squamous NSCLC. Additionally, Aurigene has multiple compounds at different stages of pre-clinical development. Aurigene has partnered with many large and mid-pharma companies in the United States and Europe and has 15 programs currently in clinical development. For more information, please visit Aurigene’s website at https://www.aurigene.com/.
CLIP
Signalling of multiple interleukin (IL)-17 family cytokines via IL-17 receptor A drives psoriasis-related inflammatory pathways
https://onlinelibrary.wiley.com/doi/10.1111/bjd.20090
M.A.X. Tollenaere,J. Hebsgaard,D.A. Ewald,P. Lovato,S. Garcet,X. Li,S.D. Pilger,M.L. Tiirikainen,M. Bertelsen,J.G. Krueger,H. Norsgaard,First published: 01 April 2021 https://doi.org/10.1111/bjd.20090Citations: 2Funding sources LEO Pharma A/S funded this study.Conflicts of interest M.A.X.T., J.H., D.A.E., P.L., S.D.P., M.L.T., M.B. and H.N. are employees of LEO Pharma. J.G.K. received grants paid to his institution from Novartis, Pfizer, Amgen, Lilly, Boehringer, Innovaderm, BMS, Janssen, AbbVie, Paraxel, LEO Pharma, Vitae, Akros, Regeneron, Allergan, Novan, Biogen MA, Sienna, UCB, Celgene, Botanix, Incyte, Avillion and Exicure; and personal fees from Novartis, Pfizer, Amgen, Lilly, Boehringer, Biogen Idec, AbbVie, LEO Pharma, Escalier, Valeant, Aurigene, Allergan, Asana, UCB, Sienna, Celgene, Nimbus, Menlo, Aristea, Sanofi, Sun Pharma, Almirall, Arena and BMS.Data Availability Statement The gene array dataset described in this publication has been deposited in NCBI’s Gene Expression Omnibus and is accessible through GEO Series accession number GSE158448 (https://www.ncbi.nlm.nih.gov/geo/query/acc.cgi?acc=GSE158448).
CLOP
https://www.drugdiscoverychemistry.com/Anti-Inflammatories/16
10:35 Small Molecule Inhibitors of RORgamma and IRAK4 for the Treatment of Autoimmune Disorders
Susanta Samajdar, Ph.D., Director, Medicinal Chemistry, Aurigene Discovery Technologies Limited
Although biologics such as anti-TNFα antibody are fairly successful in the treatment of autoimmune disorders, there is significant unmet need due to heterogeneity in diseases and lack of response to established therapies in some patients. While biologics typically target one cytokine signaling pathway, small molecule therapeutics directed towards intracellular target(s) can interfere in the signaling from multiple cytokines potentially leading to improved response. Development of small molecule oral inhibitors of IRAK4 and RORgamma to target TLR/IL-R and Th17 pathway respectively will be discussed.
PATENT
2448/CHE/2015 15.05.2015 IN
PATENT
PATENT
This application claims the benefit of Indian provisional application number 5641/CHE/2013 filed on 06th December 2013 which hereby incorporated by reference.
PATENT
- KOTRABASAIAH UJJINAMATADA, Ravi
- PANDIT, Chetan
2049005-13-0
2-Quinolinecarboxamide, 6-(2,6-dimethyl-4-pyrimidinyl)-N-[[4-(ethylsulfonyl)phenyl]methyl]-5,6,7,8-tetrahydro-6-methyl-5-oxo-, (6S)-
Molecular Weight492.59, C26 H28 N4 O4 S

EXAMPLE
PATENT
CLIP
https://www.sciencedirect.com/science/article/abs/pii/S0223523419301011
2013239366 CA 170

NEW DRUG APPROVALS
ONE TIME
$10.00
///////////////////////AUR 101, AURIGENE, ROR, IL-17, PHASE 2, CDSCO, Ravi Ujjinamatada, KOTRABASAIAH UJJINAMATADA Ravi, PANDIT Chetan, AUR101-201, plaque-type psoriasis

Ravi Ujjinamatada
VX 148

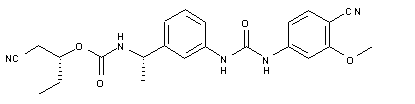
VX 148
297730-05-3
Name: VX-148
CAS#: 297730-05-3
Chemical Formula: C23H25N5O4
Exact Mass: 435.19065
Molecular Weight: 435.48
Elemental Analysis: C, 63.44; H, 5.79; N, 16.08; O, 14.70
Molecular Weight | 435.48 |
Formula | C23H25N5O4 |
CAS No. | 297730-05-3 (VX 148); |
Chemical Name | Carbamic acid, N-[(1S)-1-[3-[[[(4-cyano-3-methoxyphenyl)amino]carbonyl]amino]phenyl]ethyl]-, (1R)-1-(cyanomethyl)propyl ester |
- OriginatorVertex Pharmaceuticals
- ClassAntipsoriatics
- Mechanism of ActionInosine monophosphate dehydrogenase inhibitors
- DiscontinuedPsoriasis; Transplant rejection; Viral infections
- 13 Nov 2003Interim data from a media release have been added to the adverse events and Skin Disorders therapeutic trials sections
- 23 May 2003Vertex Pharmaceuticals has completed enrolment in a phase IIa trial for Psoriasis in Iceland
- 24 Dec 2002Phase-II clinical trials in Psoriasis in Iceland (unspecified route)
VX-148 is a second-generation, orally administered inhibitor of inosine monophosphate dehydrogenase (IMPDH). The IMPDH enzyme plays a key role in regulating immune response and proliferation of specific cell types, including lymphocytes. VX-148 is a developed for the treatment of autoimmune diseases.
Investigated for use/treatment in autoimmune diseases, psoriasis and psoriatic disorders, and viral infection.
VX-148 is a novel, uncompetitive IMPDH inhibitor with a K(i) value of 6 nM against IMPDH type II enzyme. VX-148 is slightly more potent than mycophenolic acid and VX-497 in inhibiting the proliferation of mitogen-stimulated primary human lymphocytes (IC(50) value of ~80 nM). The inhibitory activity of VX-148 is alleviated in the presence of exogenous guanosine. VX-148 does not inhibit proliferation of nonlymphoid cell types such as fibroblasts, indicating selectivity for inhibition of IMPDH activity. VX-148 is orally bioavailable in rats and mice; oral administration of VX-148 inhibits primary antibody response in mice in a dose-dependent manner with an ED(50) value of 38 mg/kg b.i.d. VX-148 significantly prolongs skin graft survival at 100 mg/kg b.i.d. in mice.
SYN
WO 0056331
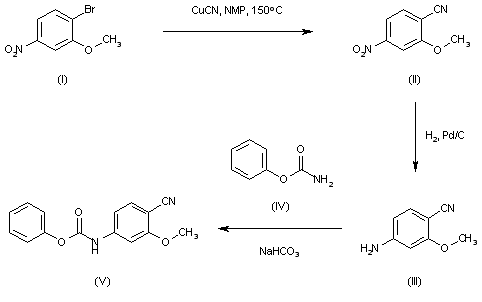
The intermediate carbamate (V) has been obtained as follows. The reaction of 4-bromo-3-methoxynitrobenzene (I) with CuCN in NMP at 150 C gives 2-methoxy-4-nitrobenzonitrile (II), which is reduced with H2 over Pd/C in ethyl acetate to yield 4-amino-2-methoxybenzonitrile (III). Finally, this compound is condensed with phenyl carbamate (IV) by means of NaHCO3 in ethyl acetate to afford the desired carbamate intermediate (V).
SYN

The reduction of 3-nitroacetophenone (VI) by means of NaBH4 in ethanol gives 1-(3-nitrophenyl)ethanol (VII), which is treated with DPPA and DBU in hot toluene to yield the azido derivative (VIII). The reduction of (VIII) with PPh3 in THF/water affords 1-(3-nitrophenyl)ethylamine (IX) as a racemic mixture that is submitted to optical resolution with L-(+)-tartaric acid to provide the desired (S)-isomer (X). The reduction of the nitro group of (X) by means of H2 over Pd/C in methanol gives 1(S)-(3-aminophenyl)ethylamine (XI), which is condensed with 2(R)-hydroxypentanenitrile (XII) and CDI to yield the carbamate (XIII). Finally, this compound is condensed with intermediate carbamate (V) by means of TEA in hot ethyl acetate to afford the target urea.
- Jain J, Almquist SJ, Heiser AD, Shlyakhter D, Leon E, Memmott C, Moody CS, Nimmesgern E, Decker C: Characterization of pharmacological efficacy of VX-148, a new, potent immunosuppressive inosine 5′-monophosphate dehydrogenase inhibitor. J Pharmacol Exp Ther. 2002 Sep;302(3):1272-7. [Article]
////////////VX 148, phase 2
O=C(O[C@H](CC)CC#N)N[C@H](C1=CC=CC(NC(NC2=CC=C(C#N)C(OC)=C2)=O)=C1)C

NEW DRUG APPROVALS
one time
$10.00
VX- ? (3-[2-(4-fluorophenyl)-lH-indol-3-yl]-N-[(3S,4R)-4-hydroxy-2- oxo-pyrrolidin-3-yl ] propanamide)
VX- ?
CAS 2446817-72-5
HYDRATE 2446818-26-2
Acetic acid, 1-methylethyl ester 2446818-27-3
C21 H20 F N3 O3, 381.4
1H-Indole-3-propanamide, 2-(4-fluorophenyl)-N-[(3S,4R)-4-hydroxy-2-oxo-3-pyrrolidinyl]-
3-[2-(4-fluorophenyl)-lH-indol-3-yl]-N-[(3S,4R)-4-hydroxy-2- oxo-pyrrolidin-3-yl ] propanamide
use in treating focal segmental glomerulosclerosis (FSGS) and/or non-diabetic kidney disease (NDKD).

NEW DRUG APPROVALS
one time
$10.00
PATENT
SOLID FORMS OF APOL1 INHIBITOR AND METHODS OF USING SAME
Compound I is disclosed as Compound 87 in U.S. Provisional Application No.62/780,667 filed on December 17, 2018, U.S. Application No. 16/717,099 filed onDecember 17, 2019, and PCT International Application No. PCT/US2019/066746 filed on December 17, 2019, the entire contents of each of which are incorporated herein by reference.
Compound I, which can be employed in the treatment of diseases mediated by APOLl, such as FSGS and NDKD
Example 1. Synthesis of Compound
Preparation of Compound I and Forms Thereof
Compound I Compound I /‘– PrOAc solvate Form A
n-pentanol/
n-heptane
Compound I
Form B
Step 1. Synthesis of 3-[2-(4-fluorophenyl)-lH-indol-3-yl]propanoic acid (C101)
[00156] To a mixture of C104 (100.0 g, 1.0 equiv) and phenyl hydrazine hydrochloride (72.2 g, 1.05 eqiv) was charged AcOH (800 mL, 8 vol). The mixture was agitated and heated to 85 °C for 16 hours. The batch was cooled to 22 °C. A vacuum was applied and the batch distill at <70 °C to ~3 total volumes. The batch was cooled to 19- 25 °C. The reactor was charged with iPrOAc (800 mL, 8 vol) and then charged with water (800 mL, 8 vol). The internal temperature was adjusted to 20 – 25 °C and the biphasic mixture was stirred for no less than 0.5 h. Stirring was stopped and the phases allowed to separate for no less than 0.5 h. The lower aqueous layer was removed. 1 N HC1 (500 mL, 5 vol) was charged to the reactor. The internal temperature was adjusted to 20 – 25 °C, and the
biphasic mixture was stirred for no less than 0.5 h. Stirring was stopped and phases were allowed to separate for no less than 0.5 h. The lower aqueous layer was removed. The reactor was charged with 1 N HC1 (500 mL, 5 vol). The internal temperature was adjusted to 20 – 25 °C, and the biphasic mixture was stirred for no less than 0.5 h. Stirring was stopped and phases were allowed to separate for no less than 0.5 h. The lower aqueous layer was removed. Water (500 mL, 5 vol) was charged to the reactor. The internal temperature was adjusted to 20 – 25 °C, and the biphasic mixture was stirred for no less than 0.5 h. Stirring was stopped and phases were allowed to separate for no less than 0.5 h. The lower aqueous layer was removed. Water (500 mL, 5 vol) was charged to the reactor. The internal temperature was adjusted to 20 – 25 °C, and the biphasic mixture was stirred for no less than 0.5 h. Stirring was stopped and phases were allowed to separate for no less than 0.5 h. The lower aqueous layer was removed. The organic phase was distilled under vacuum at <75 °C to 3 total volumes. The reactor was charged with toluene (1000 mL, 10 vol). The organic phase was distilled under vacuum at <75 °C to 5 total volumes. The reactor was charged with toluene (1000 mL, 10 vol). The organic phase was distilled under vacuum at <75 °C to 5 total volumes. The resulting slurry was heated to an internal temperature of 85 °C until complete dissolution of solids was achieved. The mixture was allowed to stir for 0.5 h at 85 °C and then cooled to an internal temperature of 19 – 25 °C over 5 h. The mixture was allowed to stir at 25 °C for no less than 2 h. The slurry was filtered. The filter cake was washed with toluene (1 x 2 vol (200 mL) and 1 x 1.5 vol (150 mL)). The solids were dried under vacuum with nitrogen bleed at 60 °C to afford product C101 (95.03 g, 70%).
Step 2. Synthesis of Compound I
[00157] A mixture of 3-[2-(4-fluorophenyl)-lH-indol-3-yl]propanoic acid C101 (50 g, 1.0 equiv), S2 hydrochloride (28.3 g, 1.05 equiv), and CDMT (34.1 g, 1.1 equiv) was charged with 2-MeTHF (200 mL, 4 vol) and DMF (50 mL, 1 vol) and the mixture was agitated. The internal temperature adjusted to <13 °C. The reactor was charged with NMM (64.5 g, 3.5 equiv) over 1 h, while maintaining internal temperature <20 °C. The internal temperature was adjusted to 25 °C and the batch was stirred at that temperature for 14 h. The batch was cooled to 10 °C and charged with water (250 mL, 5 vol) while keeping the internal temperature <20 °C. The batch was then warmed to 20 – 25 °C. Stirring was stopped, and the phases allowed to separate for 10 min. The lower aqueous phase was removed. The aqueous layer was back extracted with 2-MeTHF (2 x 200 mL, 2 x 4 vol) at
20 – 25 °C. The combined organic phases were washed with 1 N HC1 (500 mL, 10 vol) at 20 – 25 °C by mixing for 10 min and settling for 10 min. The lower aqueous phase was removed. The organic phases were washed with 0.25 N HC1 (2 x 250 mL, 2 x 5 vol) at 20 – 25 °C by mixing for 10 min and settling for 10 min for each wash. Lower aqueous phases were removed after each wash. The organic phase was washed with water (250 mL, 5 vol) at 20 – 25 °C by mixing for 10 min and settling for 10 min. The reactor was charged with 20 wt % Nuchar RGC® and stirred for 4 h. The reaction mixture was filtered through a pad of celite®. The reactor and celite® pad were rinsed with 2-MeTHF. The combined organics were distilled under vacuum at <50 °C to 5 total volumes. The reactor was charged with iPrOAc (500 mL, 10 vol). The organic phase was distilled under vacuum at <50 °C to 5 total volumes. The mixture was charged with additional iPrOAc (400 mL, 8 vol) and distillation under vacuum was repeated. The mixture was charged with additional iPrOAc (250 mL, 5 vol), heated to an internal temperature of 75 °C and stirred for 5 h. The slurry was cooled to 25 °C, over 5 h and stirred for no less than 12 h. The slurry was filtered and the filter cake washed with iPrOAc (2 x 50 mL, 2 x 1 vol). The solids were dried under vacuum with nitrogen bleed at 55 – 60 °C to afford Compound I as an iPrOAc solvate (60.38 g including 9.9% w/w iPrOAc, 80.8% yield).
Recrystallization to Form A of Compound I
[00158] Compound I as an iPrOAc solvate (17.16 g after correction for iPrOAc content, 1.0 equiv) was charged to a reactor. A mixture of IP A (77 mL, 4.5 vol) and water (137 mL, 8 vol) were charged to the reactor. The slurry was heated to an internal temperature of 75 °C. The batch was cooled to an internal temperature of 25 °C over 10 h and then stirred at 25 °C for at least 12 h. The slurry was filtered. The filter cake was washed with 36/64 IP A/water (2 x 52 mL, 2 x 3 vol). The solids were dried under vacuum with nitrogen bleed at 60 °C to afford Compound I as a neat, crystalline form (Form A, 15.35 g, 89%).
[00159] The X-ray powder diffractogram of Compound I Form A (FIG. 50) was acquired at room temperature using a PANalytical Empyrean diffractometer equipped with PIXcel ID detector. The peaks are listed in Table A below.
Table A. XRPD of Form A of Compound I
|
I
PATENT
- WO2020131807
Alternative Preparation I of Compound 87 (Indole preparation route C)
Step 1. Synthesis of 2-(4-fluorophenyl)-lH-indole (C98)
[00401] To a stirred suspension of indole (5 g, 42.7 mmol) and (4- fluorophenyl)boronic acid (8.96 g, 64.0 mmol) in AcOH (200 mL) was
added Pd(OAc)2.Trimer (1.44 g, 6.4 mmol) and the mixture stirred at room temperature for 16 h under 02-balloon pressure. Then the reaction mixture was filtered through a Celite® pad, washed with EtOAc (500 mL). The filtrates were washed with water, sat. NaHC03 solution, brine solution, then dried over Na2S04 and concentrated under reduced pressure. Purification by silica gel chromatography (Gradient: 0-10 % EtOAc in heptane) yielded the product afforded 2-(4-fluorophenyl)-lH-indole (5.5 g, 61 %). ‘H NMR (300 MHz, DMSO-de) 5 11.51 (s, 1H), 7.9 (t, J = 5.4 Hz, 2H), 7.52 (d, J = 7.8 Hz, 1H), 7.39 (d, J = 8.1 Hz, 1H), 7.30 (t, J = 8.7 Hz, 2H), 7.09 (t, J = 12 Hz, 1H), 6.99 (t, J = 7.5 Hz, 1H), 6.86 (s, 1H). LCMS m/z 212.4 [M+H]+.
Step 2. Synthesis of methyl (E)-3-[2-(4-fluorophenyl)-lH-indol-3-yl]prop-2-enoate (C99)
[00402] 2-(4-fluorophenyl)-lH-indole (1.0 g, 4.76 mmol) and methyl 3,3-dimethoxypropanoate (0.81 mL, 5.7 mmol) were suspended in dichloromethane (15 mL). Trifluoroacetic acid (2.00 mL, 26 mmol) was added rapidly via syringe, resulting in a clear brown solution. The reaction mixture was heated to 40 °C for three hours. The reaction was diluted with dichloromethane (15 mL) to give an amber solution which was washed with saturated aqueous NaHCCh (25 mL) to yield a bright yellow/light amber biphasic mixture. The phases were separated and the organic layer was washed with saturated NaHCCh (30 mL), then dried (MgSCh) and filtered. The mixture was concentrated under a nitrogen stream overnight. The crude product was obtained as a yellow powder. The product was dissolved in minimum 2-MeTHF and pentane added until the suspension became lightly cloudy. The suspension was allowed to stand overnight, and the precipitate was filtered off. The filter cake was washed with heptane (2 x 15 mL), and dried in vacuo at 40 °C to afford the product as a yellow powder. Methyl (E)-3-[2-(4-fluorophenyl)-lH-indol-3-yl]prop-2-enoate (1.30 g, 86 %). ¾ NMR (300 MHz, Chloroform -if) d 8.41 (s, 1H), 8.01 – 7.95 (m, 1H), 7.92 (d, J = 16.0 Hz,
1H), 7.58 – 7.50 (m, 2H), 7.46 – 7.41 (m, 1H), 7.33 – 7.27 (m, 2H), 7.22 (t, J = 8.6 Hz, 2H), 6.59 (d, J = 16.0 Hz, 1H), 3.79 (s, 3H). LCMS m/z 295.97 [M+H]+.
Step 3. Synthesis of methyl 3-[2-(4-fluorophenyl)-lH-indol-3-yl]propanoate (CIOO)
[00403] To a solution of methyl (E)-3-[2-(4-fluorophenyl)-lH-indol-3-yl]prop-2-enoate (7 g, 0.02 mol) in EtOAc (350 mL) was added Palladium on carbon (4 g, 10 %w/w, 0.004 mol) and stirred at room temperature for 2 h under an atmosphere of H2 (bladder pressure). The reaction mixture was filtered through a pad of Celite® and washed with EtOAc (400 mL). The filtrates was concentrated to afford methyl 3-[2-(4-fluorophenyl)-lH-indol-3-yl]propanoate (7.1 g, 100 %). 1H MR (300 MHz, DMSO-<fc) 5 11.2 (s, 1H), 7.65 (q, J = 5.4 Hz, 2H), 7.54 (d, J = 8.1 Hz, 1H), 7.36 (t, J = 9.0 Hz, 3H), 7.10 (t, J = 8.1 Hz, 1H), 7.02 (t, J = 7.8 Hz, 1H), 3.53 (s, 3H), 3.10 (t, J = 15.9 Hz, 2H), 2.63 (t, J = 15.9 Hz, 2H). LCMS m/z 298.21 [M+H]+. The product was used directly in the subsequent step without further purification.
Step 4. Synthesis of 3-[2-(4-fluorophenyl)-lH-indol-3-yl]propanoic acid (C101)
[00404] To stirred solution of methyl 3-[2-(4-fluorophenyl)-lH-indol-3-yl]propanoate (14.4 g, 0.05mol) in THF (300 mL), MeOH (300 mL) and H2O (250 mL) was cooled to -10°C. LiOH.H20 (10.1 g, 0.24 mol) was slowly added in a portion-wise manner. The reaction mixture was allowed to stir at room temperature for 16 h. The mixture was
evaporated and ice cold water (200 mL) was added, pH was adjusted to pH- 2 with 1M HC1 (400 mL, Cold solution). The mixture was stirred for 10 minutes, filtered and dried to afford 3-[2-(4-fhiorophenyl)-lH-indol-3-yl]propanoic acid (12.9 g, 94 %). ‘H NMR (400 MHz, DMSCMJ) 5 12.11 (s, 1H), 11.18 (s, 1H), 7.65 (q, J = 5.2 Hz, 2H), 7.56 (d, J = 7.6 Hz, 1H), 7.36 (t, J = 8.8 Hz, 3H), 7.10 (t, J = 8 Hz, 1H), 7.01 (t, J = 8 Hz, 1H), 3.06 (t, J = 16.4 Hz, 2H), 2.55 (t, J = 16 Hz, 2H). LCMS m/z 284.21 [M+H]+.
Step 5. Synthesis of 3-[2-(4-fluorophenyl)-lH-indol-3-yl]-N-[(3S,4R)-4-hydroxy-2- oxo-pyrrolidin-3-yl ] propanamide (87)
[00405] A mixture of 3-[2-(4-fluorophenyl)-lH-indol-3-yl]propanoic acid C101 (40 g, 120.0 mmol) and (3S,4R)-3-amino-4-hydroxy-pyrrolidin-2-one (Hydrochloride salt) S2 (23.8 g, 156.0 mmol) in DMF (270 mL) was stirred at room temperature for 5 minutes. CDMT (27.2 g, 154.9 mmol) and NMM (53 mL, 482.1 mmol) were added and the mixture was stirred at room temperature for 2 h. The mixture was poured into water (140 mL) and then stirred for 1 h at room temperature, then filtered and washing the solids with water (50 mL). The solids were dissolved in 1 : 1 IP A/water (-400 mL, until all solids dissolved) with heating (reflux) and stirring. The mixture was allowed to cool slowly to room temperature overnight. The mixture was cooled to 0 oC and stirred to break up crystals for filtration. The crystals were then filtered off, rinsed with cold 1 : 1 IP A/water to afford a tan solid (45 g). The solid was dissolved in IPA (200 mL) and heated to 80 °C to dissolve the solid. Activated charcoal (10 g) was added and the mixture was heated with stirring for 30 minutes. The mixture was filtered through Celite ® and solvent removed under reduced pressure. A mixture of 40:60 IP A/water (350 mL) was added to the solid and the mixture was heated until all solids dissolved. The mixture was cooled to room temperature over 5 h. Solids precipitated within the mixture. The mixture was then cooled to 0 °C and stirred for 1 h. The solids were filtered off and air dried on funnel for 1 h, then in a vacuum at 55 °C overnight to afford the product. 3-[2-(4-fluorophenyl)-lH-indol-3-yl]-N-[(3S,4R)-4-hydroxy-2-oxo-pyrrolidin-3-yl]propanamide (36.6 g, 79 %). ¾ NMR (300 MHz, Methanol-i¾) d 7.63 (ddt, J= 8.6, 5.1, 2.7 Hz, 3H), 7.35 (dt, J= 8.1, 1.0 Hz, 1H), 7.25 – 7.16 (m, 2H), 7.11 (ddd, J= 8.1, 7.0, 1.3 Hz, 1H), 7.03 (ddd, J = 8.0, 7.0, 1.2 Hz, 1H), 4.34 (td, J= 7.6, 6.8 Hz, 1H), 4.22 (d, J= 7.7 Hz, 1H), 3.55 (dd, J= 9.9, 7.5 Hz, 1H), 3.26 – 3.18 (m, 2H), 3.10 (dd, J= 9.9, 6.8 Hz, 1H), 2.69 – 2.59 (m, 2H). LCMS m/z 382.05 [M+H]+. The
product contained 0.23 % IPA by weight by NMR (1439 ppm IPA by residual solvent analysis). Purity is 99.5 % by (qNMR).
Alternative Preparation II of Compound 87 ( Indole Preparation route D)
Step 1. Synthesis of 5-(4-fluorophenyl)-5-oxo-pentanoic acid (Cl 04)
[00406] To a stirred suspension of AlCb(13.9 g, 0.10 mol) in dichloromethane (50 mL) was added a solution of tetrahydropyran-2,6-dione (5.93 g, 0.05
mol) in dichloromethane (100 mL) at 0 °C over a period of 15 minutes and stirred for 30 min. Then to the reaction mixture was added fluorobenzene (5 g, 0.05 mol) at 0 °C over a period of 15 min, gradually allowed to room temperature and stirred for 16 h. Then the reaction mixture was added to ice water (50 mL) under stirring. The resulting solid was filtered to afford a light yellow solid. The solid was diluted with 3 % NaOH solution (50 mL) and dichloromethane (50 mL). The aqueous layer was separated and acidified with IN HC1 at 0 °C. The mixture was then extracted with EtOAc (100 mL), dried over Na2SC>4, and concentrated under reduced pressure. The solid was then washed with pentane and dried to afford 5-(4-fluorophenyl)-5-oxo-pentanoic acid as an off white solid. (6 g, 53 %). ¾ NMR (300 MHz, DMSO-^) d 12.07 (s, 1H), 8.06 (d, J = 6 Hz, 1H), 8.02 (d, J = 5.4 Hz, 1H), 7.36 (t, J = 8.7 Hz, 2H), 3.06 (t, J = 12 Hz,
2H), 2.31 (t, J = 7.2 Hz, 2H), 1.86-1.78 (m, 2H). LCMS m/z 211.18 [M+H]+.
Step 2. Synthesis of 3-[2-(4-fluorophenyl)-lH-indol-3-yl]propanoic acid (Cl 01) [00407] Phenylhydrazine (Hydrochloride salt) (375.7 g, 2.6 mol) was combined with the 5-(4-fluorophenyl)-5-oxo-pentanoic acid (507.7 g, 2.4 mol) in a 12 L three-necked round-bottomed flask equipped with an overhead stirrer, temperature probe, and reflux condenser. AcOH (5 L) was added. The stirring was initiated and ZnCk (605 g, 4.44 mol) was added. The white suspension rapidly thickened after a few minutes (due to formation of the hydrazine intermediate). Approx. 500 mL of extra AcOH was added to aid stirring. The reaction was then heated to 100 °C for three hours. The reaction was cooled to room temperature and poured into water (approx. 6 L). The mixture was extracted with EtOAc (approx 8 L). The extract was washed with water, dried
(MgS04), filtered, and evaporated in vacuo to afford a golden yellow solid. The solid was triturated with approx. 4 L of 10 % EtOAc/DCM and filtered. The filter cake was washed with 50 % dichloromethane/heptane (approx 1 L). The filter cake was dissolved in 40 % EtOAc/dichloromethane (approx. 2L) and filtered over a plug of silica gel. The plug was eluted with 40 % EtOAc/ dichloromethane until the product had been eluted (checked by TLC (25 % EtOAc/ dichloromethane)). The filtrate was evaporated in vacuo to afford 382.6 g of an off-white solid (Crop 1). All filtrates were combined and evaporated in vacuo. The remaining solid was dissolved in 10 %
EtOAc/dichloromethane (approx. 1 L) and chromatographed on a 3 kg silica gel cartridge on the ISCO Torrent (isocratic gradient of 10 % EtOAc/dichloromethane). Product fractions were combined and evaporated in vacuo to afford a yellow solid that was slurried with dichloromethane, cooled under a stream of nitrogen, and filtered. The filter cake was washed with 50 % dichloromethane/heptane and dried in vacuo to afford 244.2 g of product (Crop 2). Altogether, both crops afforded 3-[2-(4-fluorophenyl)-lH-indol-3-yl]propanoic acid (626.8 g, 93 %). ¾ NMR (300 MHz, DMSO-i/e) d 12.15 (s, 1H), 11.20 (s, 1H), 7.74 – 7.62 (m, 2H), 7.57 (d, J = 7.8 Hz, 1H), 7.47 – 7.28 (m, 3H), 7.11 (ddd, J = 8.1, 7.0, 1.2 Hz, 1H), 7.02 (ddd, J = 7.9, 7.0, 1.1 Hz, 1H), 3.17 – 2.85 (m, 2H), 2.61 – 2.52 (m, 2H) ppm. 19F NMR (282 MHz, DMSO-i/e) d -114.53 ppm. LCMS m/z 284.15 [M+H]+.
Step 3. Synthesis of 3-[2-(4-fluorophenyl)-lH-indol-3-yl]-N-[(3S,4R)-4-hydroxy-2- oxo-pyrrolidin-3-yl ] propanamide (87)
[00408] A 3-L three neck RBF under nitrogen was equipped with a 150 mL addition funnel and thermocouple, then loaded with 3-[2-(4-fluorophenyl)-lH-indol-3-yl]propanoic acid (77.2 g, 228.6 mmol), (3S,4R)-3-amino-4-hydroxy-pyrrolidin-2-one
(Hydrochloride salt) (36.6 g, 239.9 mmol) and CDMT (44.2 g, 251.7 mmol). DMF (320 mL) was added and the orange slurry was cooled to -5 °C (acetone/brine/dry ice). NMM (88 mL, 800.4 mmol) was added via a funnel over 75 minutes to keep the internal temp <0 °C. The slurry was stirred at between -10 and 0 °C for 1 hour, then allowed to warm to ambient temperature progressively over 2 hours. Additional reagents were added (10 % of the initial quantities), and the mixture was stirred overnight at ambient temperature. Water (850 mL) was added over 60 minutes, maintaining the internal temperature at <25 °C (ice bath). This slow water addition allows for complete dissolution of any visible salt before precipitation of the product. The resulting thick slurry was stirred at ambient temperature overnight. The solid was recovered by filtration and washed with water (3 x 500 mL). The solid was dried under a stream of air at ambient temperature, then purified by crystallization.
Crystallization of 3- [2-( 4-fluorophenyl)-lH-indol-3-yl ]-N-[ ( 3S, 4R)-4-hydroxy-2-oxo- pyrrolidin-3-yl ] propanamide (87)
[00409] Under nitrogen atmosphere, a 2-L, 3 -neck flask equipped with addition funnel and thermocouple was charged with a light brown suspension of the crude 3-[2-(4-fluorophenyl)-lH-indol-3-yl]-N-[(3S,4R)-4-hydroxy-2-oxo-pyrrolidin-3-yljpropanamide (89.5 g) in IPA (225 mL, 2.5 vol). The slurry was heated to 50 °C and water (675 mL, 7.5 vol) was added until near-complete dissolution of solid was observed. The temperature was adjusted to 70 °C-to achieve full dissolution, yielding a clear amber solution. After 30 minutes, the heat source was removed and the mixture was cooled to ambient temperature over the weekend, stirring gently while maintaining the nitrogen atmosphere. The solid was recovered by filtration, washed with IPA:H20 = 1 :2 (2 x 300 mL, 2 x 3.3 vol) dried under a stream of air overnight to afford the product. 3-[2-(4-fluorophenyl)-lH-indol-3-yl]-N-[(3S,4R)-4-hydroxy-2-oxo-pyrrolidin-3-yl]propanamide (84.8 g, 92 %). ¾ NMR (300 MHz, DMSO-^) d 11.19 (s, 1H), 8.23 (d, J= 7.5 Hz, 1H), 7.77 (s, 1H), 7.72 – 7.63 (m, 2H), 7.60 (d, J= 7.8 Hz, 1H), 7.41 -7.31 (m, 3H), 7.12 (ddd, J= 8.1, 7.0, 1.2 Hz, 1H), 7.03 (ddd, J= 8.0, 7.0, 1.1 Hz, 1H), 5.49 (d, J= 5.0 Hz, 1H), 4.20 – 4.06 (m, 2H), 3.38 (s, 1H), 3.11 – 3.00 (m, 2H), 2.92 (dd, J= 9.4, 6.6 Hz, 1H). LCMS m/z 382.15 [M+H]+.
Crystallization of 3- [2-( 4-fluorophenyl)-lH-indol-3-yl J-N-[ ( 3S, 4R)-4-hydroxy-2-oxo- pyrrolidin-3-yl ] propanamide (87)
[00410] A 2-L, 3-neck flask equipped with addition funnel and thermocouple was charged with a light brown suspension of the crude 3-[2-(4-fluorophenyl)-lH-indol-3- yl]-N-[(3S,4R)-4-hydroxy-2-oxo-pyrrolidin-3-yl]propanamide in IPA (225 mL, 1 vol). The slurry was heated to 50 °C and water (675 mL, 3 vol) was added until near- complete dissolution of solid observed (mL). Temperature was increased to 70 °C under nitrogen (full dissolution, yielding a clear amber solution). After 30 minutes, the heat was removed and the mixture cooled to ambient temperature over the weekend, stirring gently under nitrogen atmosphere. The solid was recovered by filtration and washed with IPAiLLO = 1 :2 (2 x 300 mL).The solid was dried under a stream of air overnight to afford the product. 3-[2-(4-fluorophenyl)-lH-indol-3-yl]-N-[(3S,4R)-4-hydroxy-2-oxo- pyrrolidin-3-yl]propanamide (84.8 g, 92 %). ¾ NMR (300 MHz, DMSO-i/e) d 11.19 (s, 1H), 8.23 (d, J= 7.5 Hz, 1H), 7.77 (s, 1H), 7.72 – 7.63 (m, 2H), 7.60 (d, J= 7.8 Hz,
1H), 7.41 – 7.31 (m, 3H), 7.12 (ddd, J= 8.1, 7.0, 1.2 Hz, 1H), 7.03 (ddd, 7= 8.0, 7.0,
1.1 Hz, 1H), 5.49 (d, J= 5.0 Hz, 1H), 4.20 – 4.06 (m, 2H), 3.38 (s, 1H), 3.11 – 3.00 (m, 2H), 2.92 (dd, J= 9.4, 6.6 Hz, 1H). LCMS m/z 382.15 [M+H]+.
Large Scale Preparation of Compound 87
/- PrOAc solvate Form A
Step 1. Synthesis of 3-[2-(4-fluorophenyl)-lH-indol-3-yl]propanoic acid (C101)
[00411] To a mixture of C104 (100.0 g, 1.0 equiv) and phenyl hydrazine hydrochloride (72.2 g, 1.05 eqiv) was charged AcOH (800 mL, 8 vol). The mixture was agitated and heated to 85 °C for 16 hours. The batch was cooled to 22 °C. A vacuum was applied and the batch distill at <70°C to ~3 total volumes. The batch was cooled to 19- 25 °C. The reactor was charged with iPrOAc (800 mL, 8 vol) and then charged with water (800 mL, 8 vol). The internal temperature was adjusted to 20 – 25 °C and the biphasic mixture was stirred for no less than 0.5 h. Stirring was stopped and the phases allowed to separate for no less than 0.5 h. The lower aqueous layer was removed. 1 N HC1 (500 mL, 5 vol) was charged to the reactor. The internal temperature was adjusted to 20 – 25 °C, and the biphasic mixture was stirred for no less than 0.5 h. Stirring was stopped and phases were allowed to separate for no less than 0.5 h. The lower aqueous layer was removed. The reactor was charged with 1 N HC1 (500 mL, 5 vol). The internal temperature was adjusted to 20 – 25 °C, and the biphasic mixture was stirred for no less than 0.5 h.
Stirring was stopped and phases were allowed to separate for no less than 0.5 h. The lower aqueous layer was removed. Water (500 mL, 5 vol) was charged to the reactor.
The internal temperature was adjusted to 20 – 25 °C, and the biphasic mixture was stirred for no less than 0.5 h. Stirring was stopped and phases were allowed to separate for no less than 0.5 h. The lower aqueous layer was removed. Water (500 mL, 5 vol) was charged to the reactor. The internal temperature was adjusted to 20 – 25 °C, and the biphasic mixture was stirred for no less than 0.5 h. Stirring was stopped and phases were allowed to separate for no less than 0.5 h. The lower aqueous layer was removed. The organic phase was distilled under vacuum at <75 °C to 3 total volumes. The reactor was charged with toluene (1000 mL, 10 vol). The organic phase was distilled under vacuum at <75 °C to 5 total volumes. The reactor was charged with toluene (1000 mL, 10 vol). The organic phase was distilled under vacuum at <75 °C to 5 total volumes. The resulting slurry was heated to an internal temperature of 85 °C until complete dissolution of solids was achieved. The mixture was allowed to stir for 0.5 h at 85 °C and then cooled to an internal temperature of 19 – 25 °C over 5 h. The mixture was allowed to stir at 25 °C for no less than 2 h. The slurry was filtered. The filter cake was washed with toluene (1 x 2 vol (200 mL) and 1 x 1.5 vol (150 mL)). The solids were dried under vacuum with nitrogen bleed at 60 °C to afford product C101 (95.03 g, 70%).
Purification of Compound 87 by Recrystallization to Form A
[00412] Compound 87 as an iPrOAc solvate (17.16 g after correction for iPrOAc content, 1.0 equiv) was charged to a reactor. A mixture of IP A (77 mL, 4.5 vol) and water (137 mL, 8 vol) were charged to the reactor. The slurry was heated to an internal temperature of 75 °C. The batch was cooled to an internal temperature of 25 °C over 10 h and then stirred at 25 °C for at least 12 h. The slurry was filtered. The filter cake was washed with 36/64 IP A/water (2 x 52 mL, 2 x 3 vol). The solids were dried under vacuum with nitrogen bleed at 60 °C to afford Compound 87 as a neat, crystalline form (Form A, 15.35 g, 89%).
Synthetic Procedure
[00413] A mixture of 3-[2-(4-fluorophenyl)-lH-indol-3-yl]propanoic acid C101 (50 g, 1.0 equiv), S2 hydrochloride (28.3 g, 1.05 equiv), and CDMT (34.1 g, 1.1 equiv) was charged with 2-MeTHF (200 mL, 4 vol) and DMF (50 mL, 1 vol) and the mixture was agitated. The internal temperature adjusted to <13 °C. The reactor was charged with NMM (64.5 g, 3.5 equiv) over 1 h, while maintaining internal temperature <20 °C. The internal temperature was adjusted to 25 °C and the batch was stirred at that temperature for 14 h. The batch was cooled to 10 °C and charged with water (250 mL, 5 vol) while keeping the internal temperature <20 °C. The batch was then warmed to 20 – 25 °C. Stirring was stopped, and the phases allowed to separate for 10 min. The lower aqueous phase was removed. The aqueous layer was back extracted with 2-MeTHF (2 x 200 mL, 2 x 4 vol) at 20 – 25 °C. The combined organic phases were washed with 1 N HC1 (500 mL, 10 vol) at 20 – 25 °C by mixing for 10 min and settling for 10 min. The lower aqueous phase was removed. The organic phases were washed with 0.25 N HC1 (2 x 250 mL, 2 x 5 vol) at 20 – 25 °C by mixing for 10 min and settling for 10 min for each wash. Lower aqueous phases were removed after each wash. The organic phase was washed with water (250 mL, 5 vol) at 20 – 25 °C by mixing for 10 min and settling for 10 min. The reactor was charged with 20 wt % Nuchar RGC® and stirred for 4 h. The reaction mixture was filtered through a pad of celite®. The reactor and celite® pad were rinsed with 2-MeTHF. The combined organics were distilled under vacuum at <50 °C to 5 total volumes. The reactor was charged with iPrOAc (500 mL, 10 vol). The organic phase was distilled under vacuum at <50 °C to 5 total volumes. The mixture was charged with additional iPrOAc (400 mL, 8 vol) and distillation under vacuum was repeated. The mixture was charged with additional iPrOAc (250 mL, 5 vol), heated to an internal
temperature of 75 °C and stirred for 5 h. The slurry was cooled to 25 °C, over 5 h and stirred for no less than 12 h. The slurry was filtered and the filter cake washed with iPrOAc (2 x 50 mL, 2 x 1 vol). The solids were dried under vacuum with nitrogen bleed at 55 – 60 °C to afford Compound 87 as an iPrOAc solvate (60.38 g including 9.9% w/w iPrOAc, 80.8% yield).
Form A of Compound 87
[00414] Compound 87 hydrate form was converted to the dehydrated, neat crystalline form (Form A) after drying.
Hydrate Form A of Compound 87
[00415] A mixture of IP A (4.5 vol) and water (8 vol) was added to compound 87
(iPrOAc solvate containing ~2.5 – 11 wt% iPrOAc, 1.0 equiv). The slurry was heated to an internal temperature of 75 °C and filtered hot. The filtrate was cooled to 25 °C for at least 12 h. The slurry was filtered. The filter cake was washed with 36/64 IP A/water (2 x 3 vol). The solids were dried under vacuum with nitrogen bleed at 55 – 60 °C. The product was isolated as Hydrate form.
IPAC Solvate of Compound 87:
[00416] The large scale synthesis described above provided an iPrOAc solvate containing ~2.5 – 11 wt% iPrOAc after drying.
Amorphous Form of Compound 87
[00417] ~lg of compound 87 was dissolved in 22mL of acetone. The solution was evaporated using a Genevac. The resulted solid was dried at 60C under vacuum overnight. The dried solid was amorphous form.
Publication Number | Title | Priority Date | Grant Date |
---|---|---|---|
WO-2020131807-A1 | Inhibitors of apol1 and methods of using same | 2018-12-17 | |
US-2020377479-A1 | Inhibitors of apol1 and methods of using same | 2018-12-17 |
///////////
O=C(N[C@@H]1C(=O)NC[C@H]1O)CCc1c2ccccc2[NH]c1c1ccc(F)cc1
SIMILAR

predicted
VX 147
cas 2446816-88-0 predicted
O=C(N[C@@H]1C(=O)NC[C@H]1O)CCc1c2cc(F)cc(F)c2[NH]c1c1ccc(F)cc1
- OriginatorVertex Pharmaceuticals
- ClassSmall molecules; Urologics
- Mechanism of ActionApolipoprotein L1 inhibitors
- Orphan Drug StatusNo
- New Molecular EntityYes
Highest Development Phases
- Phase IIFocal segmental glomerulosclerosis
- Phase IKidney disorders
Most Recent Events
- 14 Apr 2020Phase-II clinical trials in Focal segmental glomerulosclerosis in USA (PO) (EudraCT2020-000185-42) (NCT04340362)
- 31 Dec 2019Vertex Pharmaceuticals completes phase I clinical trial in Focal segmental glomerulosclerosis and Kidney disorders (In volunteers) in USA (PO)
- 05 Aug 2019Vertex Pharmaceuticals plans a phase II proof-of-concept trial for focal segmental glomerulosclerosis in 2020
NCT Number ICMJE | NCT04340362 |
---|---|
Other Study ID Numbers ICMJE | VX19-147-101 2020-000185-42 ( EudraCT Number ) |